Fertigung (Los)
Mit dem Modul Fertigung können Sie Ihrer Fertigungsaufträge verwalten. In HELIUM 5 nennen wir einen Fertigungsauftrag Los. Den Zusammenhang zwischen Stückliste und Los finden Sie im Kapitel Zusammenhang zwischen Fertigung und Stückliste erklärt. Information zu Drucken von Planungen und Auswertungen finden Sie im Kapitel Journale und Auswertungen. Information zur Reihung der Aufgaben finden Sie im Kapitel Anzeige der nächsten Fertigungsschritte.
Status
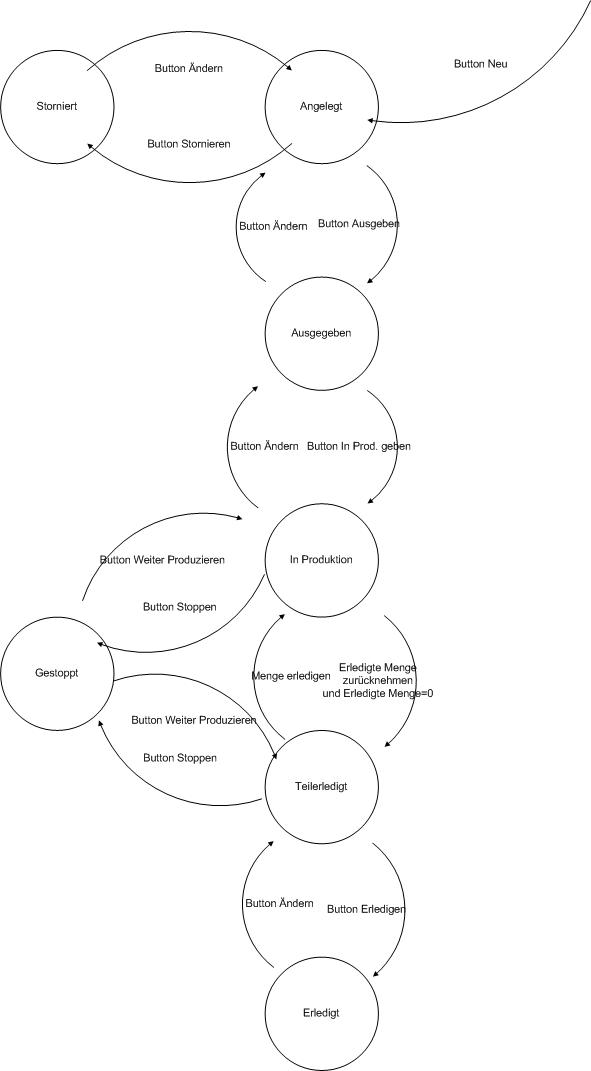
Zusammenhang von Los und Material in Abhängigkeit vom Losstatus
Losstatus | Materialsituation | Material buchen | Zeit buchen | Fehlmengen |
---|---|---|---|---|
angelegt | Das Sollmaterial des Loses wird reserviert zum Losbeginntermin, eventuell versetzt um den Beginnterminoffset der jeweiligen Position. | |||
ausgegeben | Alles vorhandene Material ist vom Lager ins Los gebucht (Ausnahme Einstellung Materialbuchung bei Ablieferung). |
| ||
in Produktion | wie ausgegeben |
| ||
teilabgeliefert | Materialsätze von bereits produzierten Mengen sind verbraucht. Produzierte Mengen sind dem Lager zugebucht. |
| ||
erledigt | Das gesamte benötigte Material ist verbraucht. Alle produzierten Mengen sind dem Lager zugebucht. | Sollten noch Fehlmengen im Los gebucht gewesen sein, so sind diese |
Ist ein Los angelegt, so ist das Material zum Losbeginntermin reserviert. Gegebenenfalls verwenden Sie zur besseren Steuerung den Parameter AUTOMATISCHE_ERMITTLUNG_BEGINNTERMINOFFSET.
Ist ein Los ausgegeben, in Produktion oder teilabgeliefert, so wurde das Material entweder vom Lager entnommen oder es gibt Fehlmengen, die den Bedarf zum Losbeginntermin aufzeigen. Fehlmengen werden beim Wareneingang bevorzugt behandelt.
Die Fehlmenge bleibt solange, bis die Ware ins Los gebucht wurde oder das Los wurde erledigt.
Anzeige der Lose (Reiter Auswahl)
Filterung der angezeigten Lose
Neben den Direktfiltern, mit denen man direkt auf ausgewählte Lose zugreift, steht auch der Filter auf den Losstatus zur Verfügung. Damit wird nach den folgenden Status gefiltert:
Alle: Es werden die Lose aller Status angezeigt
Offene: Es werden nur die offenen Lose angezeigt. Offene Lose sind alle Lose im Status angelegt, Ausgegeben, in Produktion, Teilerledigt
Zu produzieren: Es werden nur die Lose der Status Ausgegeben, in Produktion, Teilerledigt angezeigt.
Der Standard des Filters ist Zu produzieren. Die Standardeinstellung kann als Eigenschaft des Arbeitsplatzes in den Arbeitsplatzparametern mit dem Parameter FERTIGUNG_ANSICHT_OFFENE_LOSE gesteuert werden.
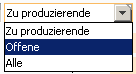
Filterung auf Status
Parameter für die Anzeige
AUFTRAG_STATT_ARTIKEL_IN_AUSWAHLLISTE
Stellen Sie den Parameter AUFTRAG_STATT_ARTIKEL_IN_AUSWAHLLISTE auf 1, wenn Sie anstelle der Artikelnummer und der Artikelbezeichnung die Auftragsnummer und das Projekt des Auftrags angezeigt bekommen möchten.
KUNDE_STATT_BEZEICHNUNG_IN_AUSWAHLLISTE
Stellen Sie den Parameter KUNDE_STATT_BEZEICHNUNG_IN_AUSWAHLLISTE auf 1, wenn Sie anstelle der Artikelbezeichnung den Kundenname aufgrund des Auftrags angezeigt bekommen möchten.
AUFTRAG_STATT_ARTIKEL_IN_AUSWAHLLISTE und KUNDE_STATT_BEZEICHNUNG_IN_AUSWAHLLISTE können nicht gemeinsam verwendet werden.
ENDE_TERMIN_STATT_BEGINN_ANZEIGEN
Stellen Sie den Parameter ENDE_TERMIN_STATT_BEGINN_ANZEIGEN auf 1, wenn Sie anstelle des Beginntermines den Endetermin angezeigt bekommen möchten.
Ausrufezeichen neben dem Status
Bei einer Ablieferbuchung durch das Terminal bzw. einer mobilen Buchung wird versucht den aktuellen Ablieferpreis zu errechnen. Konnte dies nicht durchgeführt werden, wird neben dem Losstatus der Zusatzstatus Ablieferpreis angezeigt. Diese bedeutet, dass von der Ablieferautomatik der Ablieferpreis nicht errechnet werden konnte und daher die Preisaktualisierung der Ablieferung manuell durchgeführt werden sollte. Die Details, wann dies versucht wurde, finden Sie im Reiter Zusatzstatus. Hier wird das Datum angezeigt, zu dem dieses Verhalten festgestellt wurde. Zum Beheben wechseln Sie bitte in den Reiter Ablieferung und klicken auf Ablieferpreis neu errechnen. Ev. sollten Sie, nach gültiger Berechnung des neuen Ablieferpreises den Zusatzstatus entfernen.

Los anlegen
Um ein neues Los anzulegen, klicken Sie auf den Neu Button und definieren Sie die Daten des Loses. Beim Speichern des Loses werden die aktuellen Stücklistendaten in das Los übernommen und alle Artikel, mit Ausnahme der Arbeitszeitartikel, reserviert. Arbeitszeitartikel werden in den Reiter Zeitdaten übernommen. Der Reservierungstermin ist der Beginntermin des Loses.
Losnummer mit Auftragsbezug
Gegebenenfalls soll die Losnummer sehr eng mit der Auftragsnummer korrelieren. Es kann daher mit dem Parameter LOSNUMMER_AUFTRAGSBEZOGEN = 1 diese Verbindung hergestellt werden. Dies bewirkt eine Losnummer mit folgendem Aufbau: JJ/AAAAA-PPP. JJ ist das Jahr, AAAAA die letzten fünf Stellen der Auftragsnummer, PPP die laufende Nummer der Auftragsposition.
Da trotzdem manche freie Lose, also Lose ohne Auftragsbezug angelegt werden müssen, steht für diese Definition der Parameter LOS_BELEGNUMMERNSTARTWERT_FREIE_LOSE zur Verfügung. Dieser Startwert wird bei jedem Jahreswechsel herangezogen. Dieser Startwert ist üblicherweise auf 900000000 gesetzt um zu obiger Definition zu passen.
Die Suche nach der Auftragsnummer in den Losen ist in diesem Falle so gestaltet, dass sie einfach die Auftragsnummer eingeben. Es werden alle Lose für diesen Auftrag angezeigt.
Bei der Eingabe der Losnummer ist kein - (Bindestrich) nach der Auftragsnummer möglich.
Sollte gezielt auf ein sogenanntes freies Los, also ein Los ohne Auftragsbezug gesprungen werden, so geben Sie die Losnummer vollständig ein. Wird nach Teilen einer freien Losnummer gesucht, so verwenden Sie z.B. 07/9%35. Damit werden alle freien Lose des Jahres 07 welche 35 in den nachfolgend Stellen der Losnummer beinhalten angezeigt. Also z.B. auch 07/000000350.
Losnummer mit Auftragsbezug und Losbereichen
Zusätzlich kann eine Auftragskopplung nach Bereichen realisiert werden. Stellen Sie dazu den Parameter LOSNUMMER_AUFTRAGSBEZOGEN auf 2. Die Idee dahinter ist, dass die Losnummern einerseits den Auftragsbezug haben und andererseits auch einen Bezug zu verschiedenen Bereich liefern. Daher definieren Sie bitte in der Losverwaltung unter Grunddaten die Bereiche. Bei Bereich geben Sie eine Ziffer zwischen 0-9 ein und unter Bezeichnung die von Ihnen gewünschte Bereichsbezeichnung, z.B. Mechanik, Antriebe, Software usw.
Bei der Anlage eines neuen Loses muss nun, wenn auch eine Auftragsnummer eingegeben ist (dies also kein freies Los ist), auch der Bereich eingegeben werden. Von HELIUM 5 wird dann für die Losnummer der nächste freie Zahlenbereich für die Losnummer gesucht und das Los mit dieser Nummer angelegt. Wurde ein Los versehentlich in einem falschen Bereich angelegt, so muss es im richtigen Bereich neu angelegt werden und das im falschen Bereich angelegte Los storniert oder anderweitig verwendet werden.
Der Bezug zur Auftragsposition ist in dieser Struktur nicht gegeben.
Los ausgeben
Sie finden im oberen Bereich ein Icon mit grünem Pfeil für die Losausgabe. Mit der Ausgabe werden alle Material-Positionen des Loses ausgegeben und aus dem Ursprungslager in das Los gebucht. Ist nicht ausreichend Material am Lager vorhanden, so erfolgt jeweils ein Eintrag in die Fehlmengenliste.
Durch die Statusänderung des Loses ist es ab diesem Zeitpunkt für die Zeitwirtschaft bebuchbar. Um auf ein Los Zeiten buchen zu können, muss es zumindest eine Soll-Materialposition haben. Wenn die Buchung mittels BDE-Erfassung erfolgen sollte, so muss im Los zumindest ein Arbeitszeitartikel enthalten sein, damit ein Fertigungsbegleitschein ausgedruckt werden kann.
Bei der Losausgabe gibt es im SNR-Dialog einen Haken 'Automatik'. Wenn dieser angehakt ist, werden, wenn die ausgewählte Menge gleich der benötigten Menge ist, die Seriennummern automatisch übernommen. Zum Abschluss der Losausgabe wird der Fertigungsbegleitschein und daran anschließend die Ausgabeliste ausgedruckt.
Hilfsstückliste
Beim Anlegen eines Loses werden die in einer Stückliste enthaltenen Hilfsstücklisten, mit bis zu 10 Ebenen in das Los eingebunden. Man könnte auch sagen, die Struktur wird flach gedrückt. D.h. alle Positionen der Hilfsstücklisten sind nun anstelle des Artikels der Hilfsstückliste im Los enthalten.
Bitte beachten Sie auch das im Kapitel Stücklisten zu den Hilfsstücklisten gesagte.
Hiervon ist vor allem die Einbindung der Arbeitspläne in das Los betroffen. Dieses Verhalten kann mit dem Parameter ARBEITSGAENGE_BEI_HILFSSTUECKLISTEN_VERDICHTEN gesteuert werden.
a.) 0 = Aus. Das bedeutet, es werden die Arbeitsgänge der Hilfsstücklisten an die Arbeitsgänge der Stückliste hinten angefügt. Genauer: Die durch die Überleitung entstehenden Arbeitsplanpositionen um die durch die Hilfsstückliste neu hinzukommenden Positionen ergänzt
b.) 1= Verdichten
c.) 2 Verdichten anhand Artikelgruppe
Es wird davon ausgegangen, dass hinter den Tätigkeiten, also den Arbeitszeitartikeln Artikelgruppen hinterlegt sind. Damit werden alle Tätigkeiten aus den Hilfsstücklisten in der Reihenfolge ihrer Definition, ausgehend von der Stückliste bis zur letzten Arbeitsgangposition der letzten Hilfsstückliste, in die Sollzeiten des Loses verdichtet.
Rüstzeiten und Stückzeiten werden aufsummiert. Davon ausgenommen sind Tätigkeiten die als externe Arbeitsgänge (Artikel, Bestelldaten, externer Arbeitsgang) definiert sind. Bei diesen wird die maximale Rüstzeit der jeweiligen Tätigkeit bestimmt und dieser Wert als Rüstzeit für die "verdichtete" Tätigkeit übernommen. Damit können Fremdfertigungstätigkeiten wie z.B. verzinken, lackieren, als faktisch eine externe Tätigkeit betrachtet werden. Zusätzlich wird bei dieser Einstellung der Hinweis wenn für Fremdfertigungs-Tätigkeiten kein Material (in den Positionen) zugeordnet ist, unterdrückt.
Wichtig: Die Verdichtung erfolgt nur, wenn dem Arbeitsgang KEIN Material zugeordnet ist.
Mehrere Lose zeitgleich ausgeben
Wird im Menü Bearbeiten → Mehrere Lose ausgeben gewählt, so können mehrere Lose zeitgleich ausgegeben werden. Es stehen 4 Varianten zur Wahl.
anhand Fertigungsgruppe
Sie können alle angelegten Lose anhand einer bestimmten Fertigungsgruppe in einem Durchgang ausgeben.
Es werden keine Fertigungspapiere gedruckt.
enthaltene Stücklisten
Sie können mit “enthaltene Stücklisten” alle Lose für beteiligte Stücklisten in einem Durchgang ausgeben. Enthaltene Stücklisten sind alle Unterstücklisten des markierten Loses und die Loskopfstückliste. Zum Schluss können die einzelnen Fertigungsbegleitscheine der ausgegebenen Lose gedruckt werden.
Tritt ein Fehler auf, kann die Los-Ausgabe abgebrochen werden. Alle bis dahin ausgegebenen Lose bleiben ausgegeben.
Bevor die eigentlichen Lager-Ausgabe-Buchungen durchgeführt werden, wird die Gesamtfehlmenge aller davon betroffenen Lose geprüft. Werden Fehlmengen festgestellt, so erscheint ein Dialog, in dem die dadurch entstehenden Fehlmengen angezeigt werden. In dieser Liste werden alle Artikel die Fehlmengen erzeugen würden angeführt. Mit dem GoTo kann in den jeweiligen Artikel für weitere Informationen gesprungen werden. Die Berechnungsbasis der Fehlmenge ist, Sollmenge der Materialposition größer als die Summe der Lagerstände der Los-Abbuchungsläger.
alle bis Beginntermin
Sie können mit “alle bis Beginntermin” alle Lose bis inklusive zu einem Beginntermin in einem Durchgang ausgeben. Zum Schluss werden die Fertigungsbegleitscheine ausgedruckt. Tritt ein Fehler auf, so wird die Los-Ausgabe abgebrochen, alle bis dahin ausgegebenen Lose bleiben jedoch ausgegeben.
anhand eines Auftrags
Sie können mit “anhand eines Auftrags” alle Lose eines Auftrags in einem Durchgang ausgeben.
Info:
Werden mehrere Lose gleichzeitig ausgegeben, so werden Chargen- bzw. Seriennummern tragende Artikel NICHT mit ausgegeben. Hintergrund ist die Komplexität in der Benutzerführung. Das bedeutet, dass Chargen- bzw. Seriennummern geführte Artikel als Fehlmenge in die jeweiligen Lose eingetragen werden und anschließend manuell oder mit der Ablieferbuchung ausgegeben werden müssen.
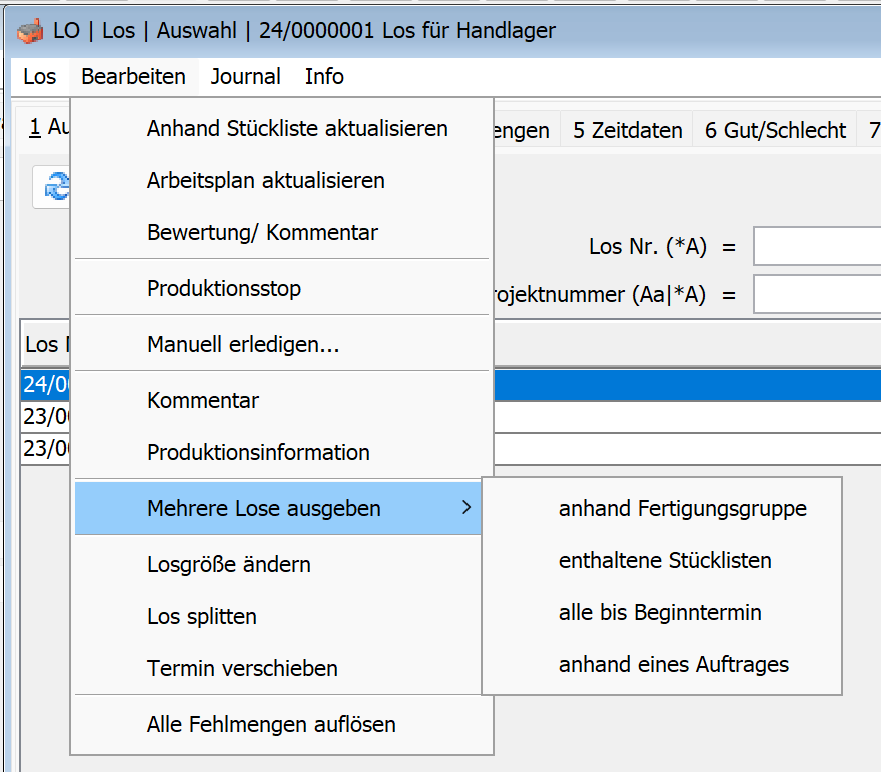
Mehrere Lose ausgeben
Schnellanlage
Gegebenenfalls möchten Sie sehr schnell Lose anlegen und sofort mit der Produktion beginnen. Die Administration mit Auftragsanlage etc. erfolgt später. Dafür haben wir die Funktion Los-Schnellanlage geschaffen.

Los Schnellanlage
Es ist dafür das Rollenrecht FERT_LOS_SCHNELLANLAGE erforderlich. Mit der Los-Schnellanlage erreichen Sie, dass bei Klick auf dieses Icon und nach Bestätigung der Abfrage sofort ein Los ohne Auftragsbezug mit Materialliste gegebenenfalls in Ihrer Fertigungsgruppe angelegt, ausgegeben und der Fertigungsbegleitschein ausgedruckt wird. Damit steht sofort ein Papier zur Verfügung auf das die Fertigungszeiten gestempelt werden können. Die eventuell nachträglich erforderliche Zuordnung zu Aufträgen verändert die Losnummer nicht mehr, auch wenn für Sie die Verbindung zwischen Losnummer und Auftragsnummer aktiviert ist (Parameter: Losnummer_Auftragsbezogen).
Losausgabe zurücknehmen
Durch Klick auf Ändern kann ein ausgegebenes Los wieder zurückgenommen werden. Das bedeutet, dass
das Material wieder dem Lager zugebucht wird und
die Positionen der Stückliste neu in das Los übernommen werden.
Die Solldaten des Loses werden automatisch aktualisiert.
Nachträglich manuell hinzugefügten Positionen sind mit einem eigenen Status (N) gekennzeichnet und werden daher auch bei der Aktualisierung der Stückliste nicht aus dem Los gelöscht.
Los stornieren
Gegebenenfalls müssen Sie ein Los stornieren. Aufgrund der relationalen Datenbank ist hier zu beachten, dass der direkte Positionsbezug im Los vor dem Storno entfernt werden muss. Gehen Sie dazu wie folgt vor:
Entfernen Sie den Positionsbezug, indem Sie auf den Reiter Kopfdaten gehen und Position klicken. Löschen Sie alle Positionen und haken Sie zur Bestätigung an.
Speichern Sie die Änderungen.
Stornieren Sie nun das Los.
Sollten Sie bereits ein Los storniert haben, ohne den Auftragsbezug zu löschen, so machen Sie zuerst das Losstorno durch Klick auf Ändern rückgängig, entfernen die Auftrags-Positions-Verknüpfung und stornieren dann anschließend das Los wieder.
Loszeiten aus der Auswahlliste buchen
Um direkt aus der Auswahlliste Beginn und Ende auf dieses Los für den angemeldeten Mitarbeiter zu buchen, kann diese Funktion durch den Parameter BEGINN_ENDE_IN_AUSWAHLLISTE der Kategorie Fertigung aktiviert werden. Damit wird durch einen Klick auf Zeiterfassung starten für den angemeldeten Benutzer ein Eintrag für dieses Los in der Zeiterfassung zum aktuellen Zeitpunkt angelegt. Mit einem Klick auf Zeiterfassung beenden wird ein Endeeintrag zum aktuellen Zeitpunkt eingetragen.
Damit die Zeiterfassungs-Icons angezeigt werden, muss der Benutzer das Recht PERS_ZEITEREFASSUNG_CUD schreiben in der Zeiterfassung besitzen.
Los mit Vertragsstrafe (Pönale)
Ist der Auftrag eines Loses mit einer Vertragsstrafe erfasst, so wird der Auftrag rot angezeigt.
Anzeige von Losen, an denen bereits gearbeitet wird
Lose, an denen bereits gearbeitet wird, werden in der Auswahlliste grün dargestellt wird.
Ist zusätzlich auf den Auftrag des Loses eine Pönale (Vertragsstrafe) hinterlegt, so wird das Los in violett dargestellt.
Bedeutung der Buchstaben in der Spalte
Mit der eigenen Spalte erhalten Sie eine Übersicht über die Verfügbarkeit und Produzierbarkeit des Loses.
Buchstabe | Losstatus | Bedeutung |
---|---|---|
<leer> | angelegt, | Keine Fehlmenge bzw. voraussichtlich keine Fehlmengen |
F | ausgegeben, | Wenigstens ein Materialartikel ist nicht in ausreichender Menge in das Los gebucht. |
L | ausgegeben, | Wenigstens ein Materialartikel ist nicht in ausreichender Menge in das Los gebucht. Das fehlende Material ist jedoch in ausreichender Menge auf dem Lager verfügbar. |
B | ausgegeben, | Wenigstens ein Materialartikel ist nicht in ausreichender Menge in das Los gebucht. Das fehlende Material ist jedoch schon bestellt und hat einen bestätigten Liefertermin. |
f | angelegt | Wenigstens ein Materialartikel ist nicht ausreichend auf Lager. Artikel einer Artikelgruppe Fremdfertigung werden ignoriert. |
b | angelegt | Wenigstens ein Materialartikel ist nicht ausreichend auf Lager. Das fehlende Material ist jedoch schon bestellt und hat einen bestätigten Liefertermin. Artikel einer Artikelgruppe Fremdfertigung werden ignoriert. |
Bei angelegten Losen wird keine ausführliche Verfügbarkeitsprüfung durchgeführt. Es wird ausschließlich der zum Zeitpunkt der Auswertung verfügbare Lagerstand betrachtet.
Art
Sie können zwischen der Losart Artikel und der Losart Materialliste wählen.
Artikel
Die Losart Artikel bedeutet, dass die Solldaten des Loses aus einer Stückliste kommen.
Materialliste
Die Losart Materialliste bedeutet, dass es keine Solldaten für das Los gibt. Sie können bei Bedarf Solldaten hinzufügen, um die Basis für eine Nachkalkulation festzulegen.
Verwenden Sie die Materialliste für Reparaturen nach Aufwand oder für allgemeine Arbeiten, deren Kosten Sie sehen möchten.
Auftrag
Geben Sie optional den Auftrag an, für den Sie produzieren.
Kunde
Geben Sie optional den Kunden an, für den Sie produzieren.
Stückliste
Wählen Sie die Stückliste des Artikels aus, der produziert werden soll.
Für jede Materialpositionen wird die Sollmenge eingetragen. Die Sollmenge berechnet sich aus der Zielmenge der Stückliste multipliziert mit der Losgröße. Ausnahme sind Rüstmengen und Rüstzeiten, diese werden nicht mit der Losgröße multipliziert, sondern 1:1 übernommen.
Weitere Steuerungen der Menge stehen mit der Verschnittbasis, dem Verschnittfaktor, der Verschnittmenge und der Fertigungs-Verpackungseinheit zur Verfügung. Eine Erklärung zur Funktionsweise des Verschnitts finden Sie im Kapitel Stücklisten.
Stückliste eines anderen Mandanten fertigen
Bei einem zentralen Artikelstamm können Stücklisten eines anderen Mandanten gefertigt werden. Gegebenenfalls muss dafür zuerst der andere Mandant und dann die Stückliste ausgewählt werden. Bei der Überleitung wird die Montageart und die Fertigungsgruppe anhand der gleichen Bezeichnung zugeordnet. Ist diese nicht gegeben, wird die erste Fertigungsgruppe / die erste Montageart verwendet. Die Überleitung der Maschinen erfolgt anhand der Maschinen ID. D.h. es wird angenommen, dass gleichwertige Maschinen auch die gleiche Maschinen ID haben. Das Ziel- und Abbuchungslager werden mit dem Hauptlager des Mandanten besetzt.
Stückliste nachträglich aktualisieren
Eine Stückliste kann manuell über Bearbeiten → Stückliste aktualisieren aktualisiert werden. Dies ist nur für Lose im Status angelegt möglich. Die Aktualisierungsbuchungen werden nur durchgeführt, wenn die Stückliste tatsächlich geändert wurde. Dies wird anhand des Anlage und Änderungsdatums des Loses bzw. der Stückliste bestimmt.
Zusätzlich wird vor der Losausgabe der Änderungsstatus der Stückliste geprüft und es erscheint ein entsprechender Hinweis. Es werden hier sowohl das Änderungsdatum des Arbeitsplans als auch der Stückliste geprüft.
Ist ein Los bei der Aktualisierung bereits im Status ausgegeben, so muss auch die Warenbewirtschaftung des Loses nachgezogen werden. D.h. wird/werden die Materiallisten der Lose aktualisiert, so wird üblicherweise auch versucht das Material zu aktualisieren. D.h. Ware die im Los überflüssig ist, da sich die Stückliste geändert hat, wird an das Lager zurückgegeben. Material welches fehlt wird versucht vom Lager zu nehmen bzw. werden Fehlmengen erzeugt. Gegebenenfalls ist es nicht erwünscht, dass diese Funktion automatisch ausgeführt wird. Stellen Sie daher hier den Parameter BEI_LOS_AKTUALISIERUNG_MATERIAL_NACHBUCHEN auf 0. Es werden damit keine Materialbewegungen durchgeführt. Die Umbuchungen sollten dann im Lagercockpit durchgeführt werden.
Bei dieser Funktion werden alle Sollmengen aktualisiert. Danach wird versucht, die Positionen mit Sollmenge 0,00 zu entfernen. Sind mit dieser Position jedoch weitere Datensätze verbunden, z.B. Bestellpositionen, so kann aus datentechnischer Sicht diese Position, auf die sie sich ja bezieht, nicht mehr gelöscht werden. Daher bleiben manchmal Positionen mit 0,00 in der Sollmenge in den Losmaterialpositionen enthalten. Gerade bei Stücklistenänderungen von sehr dynamischen Stücklisten kommt dies gerne vor.
Stückliste von der Aktualisierung sperren
Besonders bei einer laufenden Aktualisierung und Änderung von Stücklisten, gibt es im Unternehmensprozess den Zeitpunkt, bei dem die Stückliste freigegeben ist. Das bedeutet, dass ab diesem Zeitpunkt keine Änderungen der Materialpositionen und Mengen der Lose mehr gemacht werden dürfen. Um diesen Status in HELIUM 5 abzubilden gibt es im Reiter Kopfdaten das Icon Material vollständig.
Der Klick auf das Icon wird protokolliert . Nach Klick auf dieses Icon, kann keine Änderung der Soll-Materialien am Los mehr durchgeführt werden.
Arbeitsplan nachträglich aktualisieren
Der Arbeitsplan kann solange aktualisiert werden, bis das Los vollständig erledigt ist. Es wird bei der Aktualisierung so vorgegangen, dass alle Solldaten die aus den Stücklisten gekommen sind aktualisiert werden. Sind in der Stückliste Arbeitsgangpositionen hinzugekommen, so werden diese eingefügt, sind Arbeitsplanpositionen entfallen, so werden diese auf Null gesetzt. Nachträglich (N) im Los hinzugefügte Arbeitszeitpositionen werden nicht verändert.
Sollten sich wesentliche / große Teile der Solldaten des Arbeitsplans geändert haben, so löschen Sie am besten zuerst die Positionen des Arbeitsplans im Fertigungsauftrag (Reiter Zeitdaten) und wählen dann Bearbeiten, Arbeitsplan aktualisieren.
Losgröße
Geben Sie an, wie viel Sie produzieren möchten.
Nachträgliche Änderung der Losgröße
Unter dem Menüpunkt Bearbeiten → Losgröße ändern, steht Ihnen bei ausgegebenen, in Produktion befindlichen oder teilerledigten Losen die Möglichkeit der Änderung der Losgröße zur Verfügung. Die Losgröße kann sowohl erhöht als auch reduziert werden.
Bei der Änderung der Losgröße werden die Sollmengen anhand der Sollsatzgrößen neu berechnet. Danach wird geprüft, ob Material zurückgegeben werden sollte und danach werden die Fehlmengen aktualisiert.
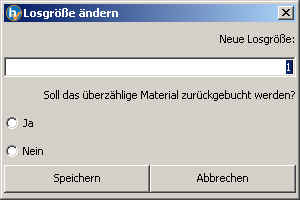
Wird das Material reduziert, so muss entschieden werden, was mit dem überzähligen Material geschehen sollte. Wird hier Ja gewählt, so wird die überzählige Menge ans Lager zurückgegeben, wird Nein gewählt, so bleibt das Material am Los und der Mehrverbrauch geht entsprechend in die Nachkalkulation ein.
Ein Los kann nur auf die bereits abgelieferte Menge reduziert werden.
Wenn die Losgröße erhöht wird, der Parameter KEINE_AUTOMATISCHE_MATERIALBUCHUNG=0 und in der Stückliste l "Materialbuchung bei Ablieferung" =0 ist, dann wird Material gemäß der Sollsatzgröße nachgebucht. Bei SNRS/CHNRS erscheint der SNR/CHNR-Dialog (gleich, wie bei der Los-Ausgabe).
Ziellager
Wählen Sie das Lager aus, in das das fertige Produkt eingebucht werden soll.
Beginn
Der Beginntermin ist der Termin, zu dem mit der Produktion begonnen werden soll.
Der Beginntermin wird bei der Neuanlage eines Loses aus einem Auftrag mit dem Auftragspositionstermin abzüglich der Kundenlieferdauer vorbesetzt. Bei Losanlage ohne Auftragsbezug wird das aktuelle Datum als Beginntermin verwendet.
Wenn der Termin nachträglich verändert werden soll, wählen Sie Menüpunkt Bearbeiten → Termin verschieben und tragen die gewünschten Termine ein. Durch Klick auf das Schloss erreichen Sie, dass die Termine gemeinsam verschoben / geändert werden.
Gegebenenfalls können Sie im Dialog weitere Lose hinzunehmen.
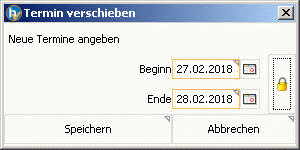
Termin verschieben
Ist die Menge positiv, ist sie zum Beginntermin im Bestellvorschlag fällig. Weitere Steuerung ist über die Parameter FRUEHZEITIGE_BESCHAFFUNG und AUTOMATISCHE_ERMITTLUNG_BEGINNTERMINOFFSET möglich.
Beginn automatisch berechnen
Setzen Sie den Parameter AUTOMATISCHE_ERMITTLUNG_AG_BEGINN auf jene Zeit, in die die Dauer eines Arbeitsganges getaktet werden sollte. Zugleich muss das Firmenzeitmodell definiert werden.
Dies bewirkt nun, dass davon ausgegangen wird, dass ein Arbeitsgang eine Loses immer nur von einem Mitarbeiter bearbeitet wird. Die Dauer des Arbeitsgangs wird auf die angegebene Stundenzahl aufgerundet und die Anzahl der Stunden und Tage passend zum Firmenzeitmodell ermittelt.
Eine übliche Einstellung sind z.B. 4 Stunden. Das ergibt bei einem üblichen Zeitmodell von 4 x 8 Stunden und 1 x 4,5 Stunden (für Freitag) 9 Blöcke für die Abarbeitung der Arbeitsgänge eines Loses. Ausgehen vom ermittelten Los-Ende-Termin wird nun der Losbeginntermin errechnet und automatisch auf diesen Termin gesetzt.
In dieser Berechnung wird auch der Betriebsurlaub berücksichtigt, sodass Sie zuerst den Betriebsurlaub im Betriebskalender (Modul Personal) definieren sollten und erst danach die Planung für die Lose machen sollten. Für diese Berechnung wird der MGZ Faktor (MitarbeiterGleichzeitig) berücksichtigt, welcher wiederum nur dann zur Verfügung steht, wenn auch die Reihenfolgenplanung aktiviert ist. Er bedeutet, dass diesen Arbeitsgang in seiner Stückzeit, mehrere Mitarbeiter gleichzeitig daran arbeiten, reduziert also die Stückzeit.
Ende
Der Endetermin ist der Termin, zu dem die Produktion voraussichtlich beendet sein wird.
Ist die Menge negativ, ist sie zum Endetermin im Bestellvorschlag fällig.
Ende automatisch berechnen
Eine Möglichkeit, die Durchlaufzeit eines Loses zu ermitteln, ist die Vorgehensweise, dass in der Stückliste für jeden Arbeitsgang der sogenannte Arbeitsgangversatz hinterlegt wird. Das bedeutet dass der Zeitversatz in Tagen vom ersten zum zweiten Arbeitsganges die organisatorische Dauer für den ersten Arbeitsgang darstellt. Damit ergibt sich die geplante Gesamtdauer für das Los. Daraus ergibt sich auch, dass hier Arbeitstage zur Anwendung kommen.
HELIUM 5 rechnet in Kalendertagen. Durch die Verwendung der Arbeitstage ergibt sich, dass bei der Anlage des Loses aber auch bei der Verschiebung des Los-Beginntermins, der Beginntermin des jeweiligen Arbeitsganges anhand des Firmenzeitmodells errechnet werden. Es muss dafür der Parameter AUTOMATISCHER_ERMITTLUNG_LOS_ENDE aktiviert werden. Dieser Parameter hat Vorrang vor dem Parameter AUTOMATISCHE_ERMITTLUNG_AG_BEGINN.
Dies bewirkt, dass für die Berechnung des tatsächlichen Starttermins des jeweiligen Arbeitsganges die Arbeitstage anhand des Firmenzeitmodells ermittelt werden. Damit können Feiertage, Betriebsurlaube u.ä. abgebildet werden. Bitte beachten Sie, dass im Firmenzeitmodell jeder Tag mit einer Sollzeit > 0 als vollwertiger Arbeitstag gerechnet wird. So wird der in Österreich übliche Freitag mit meist nur 4Std auch als voller Tag gerechnet. Daraus ergibt sich auch, dass in dieser Einstellung bei den Termineingaben nur der jeweilige Beginntermin eingegeben werden kann. Das Ende errechnet sich immer automatisch.
Dauer
Ist die Dauer angehakt, wird der Abstand zwischen Beginn und Ende nicht geändert. Wenn Sie den Beginn verändern, wird sich das Ende automatisch anpassen. Wenn Sie das Ende verändern, wird sich der Beginn automatisch anpassen.
Ist die Dauer nicht angehakt, können Sie Beginn und Ende nach Belieben verändern. Wenn Sie den Beginn verändern, hat dies keinen Einfluss auf den Endetermin. Wenn Sie das Ende verändern, hat dies keinen Einfluss auf den Beginntermin.
Durchlaufzeit und Rückwärts und Vorwärts
Die Durchlaufdauer ist die Zeit in Tagen, die es benötigt, das Produkt durch die Fertigung zu bringen. Sie wird von der Stückliste übernommen.
Wenn Sie die Durchlaufzeit ändern, müssen Sie definieren, ob der Beginntermin oder der Endetermin angepasst werden soll. Ist Vorwärts gewählt, bleibt der Beginntermin und der Endetermin wird angepasst. Ist Rückwärts gewählt, bleibt der Endetermin und der Beginntermin wird angepasst.
Bei der Internen Bestellung wird nach der Rückwärts-Terminierung vorgegangen. Die Formel wird fortgesetzt, bis die Stücklistenhierarchie vollständig aufgelöst ist.
Auftrags-Liefertermin
- Kunden-Lieferdauer der Lieferadresse des Auftrags
--------------------------------------------------------
Produktionsendtermin = Abliefertermin
- Durchlaufzeit in Kalendertagen
--------------------------------------------------------
Ergibt Produktionsstarttermin
- Fertigungsvorlaufzeit (Mandantenparameter)
--------------------------------------------------------
Produktionsendtermin des Unterloses
- Bestellungsvorlaufzeit Eigenfertigung (Mandantenparameter)
--------------------------------------------------------
gewünschter Liefertermin der Einkaufsteile
Kommentar
Der Kommentar eines Fertigungsauftrages kann jederzeit bearbeitet werden. Verwenden Sie dazu den Menüpunkt Bearbeiten, Kommentar. Der bisher eingegebene Kommentar wird direkt in den Kopfdaten angezeigt.
Produktionsinformation
Neben dem Kommentar steht für einen Fertigungsauftrag auch die Produktionsinformation zur Verfügung. Auch Sie kann jederzeit bearbeitet werden. Verwenden Sie dazu den Menüpunkt Bearbeiten, Produktionsinformation.
Geplante Materialkosten
Gegebenenfalls möchten Sie reine Material-Sollkosten für ein Los definieren. Verwenden Sie dafür das Feld in den Los-Kopfdaten. Geben Sie den Betrag in Ihrer Mandantenwährung ein.
Sind bei einem Los geplante Materialkosten definiert, so werden damit die Soll-Materialkosten in den Materialpositionen für die Nachkalkulationen deaktiviert und anstatt dessen nur die Soll-Materialkosten verwendet.
Weiters haben Sie die Möglichkeit im Reiter Material für jede einzelne Position einen Sollpreis zu definieren. Wenn ein Kalk-Preis aus der Stückliste vorhanden ist, wird dieser verwendet, auch wenn dieser 0 ist. Wenn kein Kalkpreis vorhanden ist, dann wird der Lief1Preis unter Berücksichtigung der Mengenstaffel verwendet.
Zur Aktualisierung der Preise gibt es den Button Sollpreise neu kalkulieren . Nach Klick auf das Icon werden die Preise gemäß der Informationen aus dem Artikellieferanten aktualisieren.
Material
Im Reiter Material sehen Sie eine Liste des Sollmaterials.
Lagerstand anzeigen
Durch aktivieren des Parameters LAGERINFO_IN_POSITIONEN werden in den Reitern Material und Fehlmengen zusätzlich der aktuelle Lagerstand, die Verfügbarkeit insgesamt und die bestelle Menge angezeigt. Dies vor allem, um Ihnen eine rasche Abschätzung über die Materialsituation des entsprechenden Loses zu ermöglichen. Nutzen Sie für eine weitere detaillierte Ansicht die theoretische Fehlmengenliste.
Ist in Ihrer HELIUM 5 Installation auch die Funktion der Ersatztypenverwaltung aktiviert, so wird neben dem Lagerstand der Original-Artikel auch die gesamt lagernde Menge aller direkt oder indirekt diesem Artikel zugewiesenen Ersatzartikel angezeigt. D.h. damit können Sie sehr rasch feststellen, ob Sie den Bedarf ev. durch die Ersatzartikel erfüllen können.

Anzeige Lagerstand mit Ersatztypen
Sollmaterial ändern
Im Reiter Material kann mit neu ein neuer Solleintrag im Los hinterlegt werden. Damit definieren Sie neue Solldaten und einen entsprechenden Sollpreis für die neue Losposition. Zusätzlich erfasste Sollmengen werden am linken Rand mit einem "N" angezeigt. Dass es Solldaten sind, ist am Eintrag der Menge ersichtlich.
Diese Funktion kann z.B. zur Verwendung von alternativen Artikeln oder nur einmalig freigegebenen Artikeln verwendet werden. Eine Änderung der Sollmenge ist im gesamten Bereich möglich. Die Fehlmenge wird entsprechend mitgezogen. Die angezeigte Sollsatzgröße / Sollsatzmenge wird aus der Sollmenge über die Losgröße errechnet.
Preise von nicht lagerbewirtschafteten Artikeln ändern
Üblicherweise werden z.B. für Stromkosten und ähnliche fixen Kosten nicht lagerbewirtschaftete Artikel angelegt. Diese Artikel werden gegebenenfalls in Hilfsstücklisten zusammengefasst, in die jeweilige Stückliste eingebunden und so auf das Los gebucht. Wenn nun festgestellt wird, dass bei einem bereits ausgegebenen oder erledigten Los diese Werte / Preise falsch sind, so ist folgende Vorgehensweise für die Aktualisierung des Ist-Preises im Los zielführend.
Wenn das Los noch komplett zurückgenommen werden kann, so nehmen Sie es vollständig zurück. Ändern Sie danach den Gestehungspreis des nicht lagerbewirtschafteten Artikels und geben Sie dann das Los wieder aus. Beachten Sie, dass diese Preisänderung auch für alle zukünftigen Ausgaben gilt.
Kann das Los nicht zurückgenommen werden, so gehen Sie bitte wie folgt vor:
Das Los ist im Status ausgegeben oder teilerledigt (Ablieferungen müssen dafür nicht zurückgenommen werden).
Im Reiter Material wählen Sie den gewünschten Artikel und geben diesen über Ausgabemenge ändern an das Lager zurück (die Ausgabemenge auf 0,00 setzen).
Korrigieren Sie nun den Gestehungspreis des nicht lagerbewirtschafteten Artikels.
Im Reiter Material des Loses geben Sie nun über nachträgliche Materialentnahme den Artikel wieder aus.
Damit haben Sie den richtigen Preis / Wert auf dem Los.
Einmalartikel
Gegebenenfalls benötigen Sie einmalig eine bestimmte Materialposition. Dies kann theoretisch mit einem Handartikel im Los und dann in der Bestellung usw. abgebildet werden. Soll der Artikel jedoch auch im Bestellvorschlag angezeigt werden, können Sie die Funktionalität des Einmalartikels in der Buchung von zusätzlichem Los-Soll-Material verwenden. Wenn Sie im Los mit neu weitere Sollpositionen hinzufügen, danach auf die Artikelauswahl klicken, so steht hier neben dem Neu auch die Anlage eines Einmalartikels zur Verfügung. Hier werden nur sehr wenige Erfassungsdaten für den Artikel abgefragt. Als zusätzliche Eigenschaft ist dieser Artikel grundsätzlich nach der Anlage versteckt und hat eine automatisch generierte fortlaufende Artikelnummer, welche mit ~ beginnt. Sollten Sie nun nach der Fertigung Ihres Prototypen feststellen, dass Sie diesen Artikel doch öfter benötigen, so muss lediglich das Versteckt entfernt werden und dem Artikel eine Artikelnummer Ihren Regeln entsprechend gegeben werden.

Buchung zusätzlicher Kosten ins Los
Es kommt immer wieder vor, dass ungeplante Kosten in ein Fertigungslos gebucht werden müssen. Da dies dann meistens keine Ware im eigentlichen Sinne ist, z.B. Flugtickets, müssen diese über einen kleinen Umweg eingebucht werden. Die Vorgehensweise ist wie folgt:
Legen Sie einen Artikel an, der nicht Lagerbewirtschaftet ist und als Mengeneinheit Ihre Mandantenwährung z.B. Euro hat.
Definieren Sie bei diesem Artikel den Gestehungspreis mit 1,- €
Gehen Sie in das Los, Material und buchen Sie mit Nachträgliche Materialentnahme ohne Sollposition diesen Artikel in das Ist-Material des Loses. Als Menge geben Sie den Betrag an mit dem das Los belastet werden sollte und klicken Sie auf Entnahme.
Gegebenenfalls ergänzen Sie in der Materialposition des Loses den Kommentar noch um eine weiterführende Bezeichnung, damit Sie später noch wissen welche Kosten das tatsächlich waren.
Nachträgliches Ändern bereits ausgegebener Mengen
Durch eine allgemeine Rücknahme können Sie Material aus dem Los zurück ins Lager buchen. Da dies gerade bei bereits teilerledigten / teilabgelieferten Losen nicht mehr möglich ist und da dies sehr oft nur einzelne Artikel betrifft, steht dafür die Funktion Nachträgliche Änderung bereits ausgegebener Mengen zur Verfügung. Durch Klick auf diese Knopf erscheint eine Liste der Detailbuchungen der Buchungen dieser Position von Lager ins Los. Wählen Sie eine entsprechende Ausgabeposition aus und ändern Sie im unteren Dialog die Entnahmemenge auf die gewünschte Stückzahl. Nach der Bearbeitung aller Positionen schließen Sie dieses Fenster durch Klick auf das rechte obere X. Bei dieser Änderung werden die Fehlmengen entsprechend angepasst. Mit dieser Darstellung sehen Sie auch, aus wie vielen Einzelbuchungen die Entnahmebuchung besteht.
Nachträgliche Materialentnahme
Mit dem Button im Reiter Material kann nachträglich Material auf das Los gebucht werden. Sie gelangen dadurch in einen eigenen Dialog, in dem Sie Material aus dem Lager in das Los entnehmen können. Der Dialog ist in der Sollposition mit der ausgewählten Materialposition des Loses vorbesetzt. Unter Menge wird diejenige Menge vorgeschlagen, welche Sie noch auf das Los buchen sollten und aufgrund des Lagerstandes auch können.
Sollte die Buchung die Fehlmenge reduzieren, so belassen Sie den Haken bei Fehlmenge reduzieren. Ist es erforderlich, dass die Fehlmenge erhalten bleibt, so darf hier kein Haken gesetzt sein.
Sollte es erforderlich sein, dass zusätzlich Material auf das Los gebucht werden soll, also Material dass mit der Losposition keinen Zusammenhang hat, so klicken Sie bitte auf Sollposition und löschen Sie den Bezug durch Klick. Ist keine Sollposition gewählt, so kann ein beliebiger Artikel ausgewählt werden. Zusätzlich erfasste Ist-Mengen werden am linken Rand mit einem "N" angezeigt. Dass es Ist-Daten sind, ist am Eintrag unter Ausgegeben ersichtlich.
Für Rückgaben und Erhöhung der Fehlmengen wird die bereits ausgegebene Mengen verwendet und verändert.
Mit dem Knopf Nachträgliche Materialentnahme ohne Sollposition ist die Bedienung vereinfacht. Wenn Sie auf diesen Knopf klicken, so wir ebenfalls der Dialog der nachträglichen Materialentnahme aufgerufen. Hier ist jedoch unabhängig auf welcher Zeile der Materialentnahme der Cursor steht, die Sollposition nicht vorbesetzt und somit die zusätzliche Entnahme von Material deutlich einfacher.
Ausgabe von Material mit Chargen
Sind im Material des Loses chargengeführte Artikel vorhanden, so erscheint bei der Materialausgabe eine Abfrage, welche Charge verwendet werden soll. Ist nur eine Charge lagernd, so kann nur diese eine Charge entnommen werden, weshalb keine Abfrage erscheint.
Setzen Sie den Parameter LOSAUSGABE_AUTOMATISCH auf 1, wenn HELIUM 5 automatisch eine Charge wählen soll.
Setzen Sie den Parameter AELTESTE_CHARGENNUMMER_VORSCHLAGEN auf 1, wenn immer die älteste Charge zuerst vorgeschlagen werden soll.
Material zurückgeben
Um Material an das Lager zurückzugeben, verwenden Sie im Los im Reiter Material den Knopf nachträgliche Materialentnahme. Hier ist üblicherweise Lagerabgang voreingestellt. Nehmen Sie hier nun den Haken heraus, so wird eine Lagerzugangsbuchung des gewählten Artikels mit der angegebenen Menge durchgeführt.
Bei Rückgabe des Materials über die nachträgliche Materialentnahme werden die Fehlmengen NICHT erneut in das Los eingetragen.
Ein großer Unterschied zwischen den beiden Rückgaben ist auch in Bezug auf die Pflege der Gestehungspreise gegeben. Wurde zu viel Material in ein Los entnommen, so wird dieses mit aktuellem Gestehungspreis vom Lager ins Los gebucht. Wird diese Menge über die nachträgliche Materialentnahme zurückgegeben, so wird eine Lagerzubuchung durchgeführt und dafür der zum Zeitpunkt der Zubuchung gültige Gestehungspreis verwendet. Es wird also eine weitere Zubuchung generiert. Wird nun die ursprüngliche Zubuchung, z.B. der Wareneingang verändert, so wirkt diese Veränderung bis ins Los, aber nicht mehr bei der Lagerrückgabe von Los ans Lager. Hier bleibt der alte Gestehungspreis erhalten. Dies kann soweit gehen, dass damit negative Gestehungspreise auf einem Los verursacht werden.
Müssen Mengen ans Lager zurückgegeben werden, so sollte dies in aller Regel über die Korrektur der bereits ausgegebenen Mengen durchgeführt werden. Dies hat die Eigenschaft, dass dadurch die Entnahmebuchung rückgängig gemacht wird (so als wenn es sie nie gegeben hätte) und auf Grund dessen, wirken Änderungen der ursprünglichen Zubuchung wieder wie gedacht.
Nachteil: Werden Lagerbestände und Lagerbewegungen zum Stichtag betrachtet und gehen diese Entnahmen / Rückgaben über diese Stichtagsbetrachtung, so ändert sich dadurch der Lagerstand / die Warenbewegung vor/zum Stichtag, wodurch die Betrachtung des Lagerstandes / der Warenbewegung zum nachfolgenden Stichtag verfälscht wird.
Meldung zur Konvertierung von Einheiten
Gegebenenfalls erhalten Sie eine Meldung, dass die Stücklisteneinheit nicht konvertiert werden kann. Um das Los abzuspeichern, korrigieren Sie die Positionseinheit der Stückliste.
Wenn Sie die Stücklistenposition nicht aufgrund der angezeigten Einheit erkennen können, so gehen Sie die Stücklistenpositionen durch. Auch hier erhalten Sie bei unstimmigen Einheiten die oben dargestellte Fehlermeldung.
Hinterlegen Sie berechenbare Konvertierungen einmalig. Details finden Sie im Kapitel Mengeneinheit.
Negative Sollmengen, Rückgabe ans Lager
Es werden negative Sollmengen unterstützt. Das bedeutet, dass z.B. eine Baugruppe zerlegt werden kann und die daraus gewonnen Einzelteile werden ans Lager gebucht. So könnte der Inhalt, der dieses Zerlegen beschreibt z.B. so aussehen, dass mit einer positiven Menge die Baugruppe komplett vom Lager entnommen wird und die daraus gewonnenen einzelnen Komponenten mit negativen Mengen eingetragen werden.
Die Termine wirken so, dass die positiven, vom Lager entnommenen Mengen zum Beginnzeitpunkt des Loses entnommen werden, die negativen Mengen, die also zurückgegeben werden, werden zum Ende-Zeitpunkt des Loses als zurückgebbar verwaltet. Bei der (Teil-)Ablieferung werden diese Lose ans Lager gebucht.
Die Rückgabe erfolgt immer in das erste angegebene Abbuchungslager, weiter Lager werden nicht berücksichtigt.
Fehlmengen
Mit HELIUM 5 können Sie Fehlmengen buchen, indem Sie ein Los bereits ausgeben, obwohl noch nicht das gesamte Material für diesen Fertigungsauftrag verfügbar ist.
Wird ein Artikel eingebucht, der als Fehlmenge gelistet und in einem Los benötigt wird, erhalten Sie beim Erfassen des Wareneingangs eine Information.
Eine Information über die Auslöser der Fehlmenge erhalten Sie über den Druck der Fehlteile. Wechseln Sie dazu im Los in den Reiter Fehlmengen und klicken auf das Druckersymbol. Hier erfolgt eine Auflösung in die jeweiligen Unterlose, so können Sie erkennen, welche Materialposition auslöst, dass die einzelnen Lose nicht gefertigt können.
Der Termin der Fehlmenge entspricht immer dem Produktionsstart des Loses, korrigiert um den Beginnterminoffset.
Wurde beim Warenzugang die Fehlmenge auf Lager belassen, so muss dies durch die nachträgliche Materialbuchung dem Los zugeordnet werden.
Bei der Auflösungsbuchung der Fehlmenge wird immer nur die gerade zugebuchte Menge weiter in das/die Los(e) gebucht werden. Die Buchung von bereits lagerndem Material muss mit der nachträglichen Materialentnahme durchgeführt werden.
Im Reiter Fehlmengen werden diejenigen Artikel angezeigt, die für dieses Los noch Fehlmengen sind. Ist das Los nur angelegt so sind dies theoretische Fehlmengen. D.h. hier werden hier nur Originalartikel angezeigt, deren noch auszugebende Menge (Soll - Ist) kleiner dem Lagerstand ist.
Ist der Parameter LAGERINFO_IN_POSITIONEN aktiviert (=1), so werden auch die Lagerstände angezeigt.
Ist in Ihrer HELIUM 5 Installation auch die Ersatztypenverwaltung verfügbar, so sehen Sie auch die Lagerstände aller Ersatztypen. Dafür ist definiert, dass die direkten und die indirekten Ersatztypen herangezogen werden. Direkt sind diejenigen die in der Stückliste hinterlegt sind und somit direkt in das Los übernommen wurden (die grünen Zeilen). Indirekte Ersatztypen sind diejenigen, die beim Originalartikel unter Ersatztypen zugewiesen sind. Dies vor allem, damit Sie einen Hinweis bekommen, dass ev. andere Artikel für diese Position eingesetzt werden sollten, da verfügbar.
Fehlmengen auflösen
Fehlmengen können durch zwei verschiedene Buchungen aufgelöst werden.
Automatische Fehlmengenauflösung bei Lagerzugang
Bei jedem Warenzugang wird geprüft, ob auf dem zugebuchten Artikel Fehlmengen eingetragen sind. Ist dies der Fall, so erscheint ein entsprechender Dialog, mit dem Sie die Zugangsmenge auf die verschiedenen Lose verteilen können. Dadurch werden automatisch die Lose aufgelöst. In dieser Funktion steht Ihnen auch das Markieren mehrerer Los-Zeilen zur Verfügung. Durch Klick auf markierte Zeilen auf einmal entnehmen werden die markierten Positionen gebucht.
Wird eines der HELIUM 5 Module geschlossen, so wird automatisch geprüft, ob nachträgliche Fehlmengenauflösungen gebucht wurden. Wenn ja, so erscheint eine Meldung. Beantworten Sie diese mit Ja, so kann je Los eine Liste der aufgelösten Fehlmengen gedruckt werden. Hier wird pro Los ein eigenes Blatt ausgedruckt.
Manuelle Fehlmengenauflösung
Mit der oben beschriebenen Funktion der nachträglichen Materialentnahme können bei dem angehakten Feld Fehlmenge reduzieren die entsprechenden Fehlmengen reduziert / aufgelöst werden.
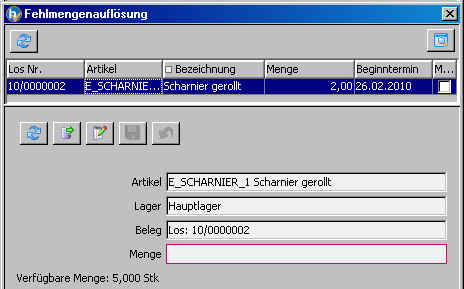
Aus verschiedenen Umständen kann es vorkommen, dass fehlende Mengen nicht (halb-) automatisch den Losen zugebucht werden. Um auch diese Daten zu sehen gibt es das Journal Auflösbare Fehlmengen. Hier sehen Sie alle Artikel und alle Lose, die Fehlmengen behaftet sind, bei deren Artikel aber Lagerstände gegeben sind.
Dringlichkeitsmarkierung
Sie haben im Los die Möglichkeit, Materialpositionen als dringend markieren zu können. Sie finden diese Möglichkeit im Reiter Material. Markieren Sie die wirklich dringenden Positionen und klicken Sie dann auf dringend. Damit werden die entsprechenden Materialpositionen als dringend markiert und in Blau dargestellt.
Im Journal Fehlmengen aller Lose kann nur Dringende angehakt werden, womit man eine Übersicht über die sofort zu beschaffenden Artikel bekommt.
Eintrefftermin
Im Reiter Fehlmengen finden Sie die Spalte Eintrefftermin. Hier wird das Datum eingetragen, zu dem Zeitpunkt man den Lagerzugang erwartet. Dieser früheste Eintrefftermin berücksichtigt zusätzlich zu den Bestellpositionen auch die zu erwartenden Losablieferung (= frühester Ende-Termin eines offenen Loses). So erhalten Sie schnell Überblick über die Engstellen oder zu kritischen Terminen, Lagerständen zum Beispiel in Unterlosen. Um etwas Sicherheit zu erreichen, wird bei den Bestellungen nur der vom Lieferanten bestätigte Termin angezeigt. D.h. Bestellungen die noch ohne eingetragener Auftragsbestätigung sind, werden hier nicht berücksichtigt.
Zeitdaten
In den Zeitdaten eines Loses kann sehr genau gesteuert werden wie dieses Los in den verschiedenen Auslastungs-/Zeitplanungen berücksichtigt werden sollte.
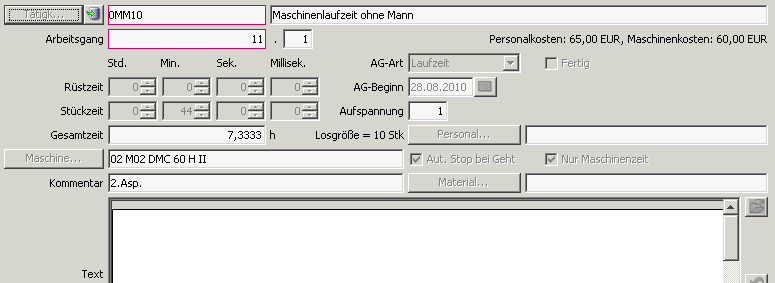
Reiter Zeitdaten
Feldname | Bedeutung |
---|---|
Tätigkeit | Tätigkeit, die durchgeführt werden soll. Für die Vorkalkulation der Personalzeiten werden die unter Artikellieferant hinterlegten Sätze verwendet. |
Arbeitsgang | Laufende Nummer des Arbeitsgangs als übergeordnete Gruppe der nachfolgenden Unterarbeitsgänge |
Unterarbeitsgang | Untergliederung eines einzelnen Arbeitsganges in weitere Schritte. Insbesondere für die Steuerung des Verhaltens der Zeiterfassungsterminals erforderlich. |
Personalkosten / Maschinenkosten | Anzeige der Soll-Kosten zu Ihrer Information |
AG-Art | Arbeitsgangart |
Gesamtzeit | Anzeige der errechneten Gesamtzeit anhand Stück- und Rüstzeit in Stunden |
AG-Beginn | Arbeitsgangbeginn. Im Unterschied zur Stückliste wird hier der Beginntermin des Arbeitsganges für jeden Arbeitsgang angegeben. Wird bei einem Arbeitsgang der Termin geändert, so werden alle nachfolgenden Arbeitsgänge ebenfalls um die Differenztage verschoben. Dies wird in beiden Richtungen durchgeführt. |
Aut.Stop bei Geht | Automatisches Stop bei Gehtbuchung des Mitarbeiters. Dieser Wert wird beim Anlegen des Arbeitsganges, des Loses von der Einstellung der Maschine übernommen und kann hier, z.B. für eine Geisterschicht, abgeändert werden. |
AG-Beginn
Mit dem Arbeitsgang-Beginn-Datum können Sie steuern, wann der Arbeitsgang (AG) begonnen wird. Somit kann ein Versatz - zum Beispiel weil ein Arbeitsgang ausgelagert zu einem anderen Unternehmen ist - abgebildet werden. Weiters steuern Sie hiermit die parallele oder serielle Durchführung von Arbeitsgängen, in dem Sie bei parallel durchführbaren AG keinen Versatz angeben.
Der intern relativ gerechnete Lostermin ist zugleich der AG-Beginn. Falls Sie nun den Arbeitsgang 4 verschieben, werden darauffolgende Arbeitsgänge ebenso weiter verschoben. Somit sehen Sie zum Beispiel die direkte Auswirkung, wenn eine Fremdfertigung mehr Tage in Anspruch nimmt als ursprünglich geplant. Die Eingaben des Arbeitsgangversatzes werden in der Auslastungsvorschau berücksichtigt. Dadurch erkennen Sie im Detail die aktuelle Situation in der Fertigung und erhalten ein essentielles Steuerungswerkzeug, um optimal die Auslastung zu planen.
Istzeitdaten
Im Reiter Istzeitdaten sehen Sie eine Zusammenfassung aller Zeiten, die bereits auf das Los erfasst sind.
Lager
Im Reiter Lager können mehrere Läger für ein Los definiert werden. Dies bewirkt, dass bei der Losausgabe zuerst das Material vom ersten Lager entnommen wird. Ist auf diesem Lager kein Material mehr verfügbar, so wird versucht, Material vom nächsten Lager zu entnehmen. Bis hin zum letzten dem Los zugeordneten Lager.
Dadurch können Sie z.B. Material von Kundenlägern, welches aber von Ihnen verwaltet wird, bevorzugt abbuchen. Erst wenn das gesamte Material des jeweiligen Artikels vom Kundenlager verbraucht wurde, wird auf Ihr eigenes Lager, wenn dies definiert ist, zurückgegriffen.
Im Artikel unter Grunddaten → Lager können die Lager definiert werden, welche automatisch als Abbuchungslager für ein neues Los vorgeschlagen werden. Geben Sie hier unter Sortierung Losausgabe die gewünschte Reihenfolge der Läger an, die als Abbuchungslager übernommen werden sollten. Wurde kein Lager definiert, so wird automatisch das Hauptlager übernommen.
Zusätzlich kann für jede Stückliste definiert werden, welche Läger ergänzend berücksichtigt werden sollten. Die Reihenfolge für das automatische Vorbesetzen der Abbuchungs-Läger für das Los ist wie folgt:
Es werden alle Läger, welche in der Stückliste definiert sind, übernommen.
Es werden alle Läger die "Sortierung Losausgabe" definiert haben, in dieser Reihenfolge übernommen.
Ist das Hauptlager noch nicht vorhanden, wird dieses ebenfalls übernommen
Um nun Fremdfertigungs-Lose komfortabel zubuchen zu können, reicht es im Wareneingang einer Bestellung das entsprechende Lieferantenlager anzugeben. Dieses kann wiederum in den Konditionen des Lieferanten definiert werden.
Ablieferung
Mit dem oberen Modulreiter Ablieferung gelangen Sie zur Funktionalität der Ablieferung der Fertigung an das Lager. Verwenden Sie die Ablieferung, um produzierte Mengen fertig zu melden.
Durch Klick auf Neu wird eine weitere Teilerledigung des Loses durchgeführt. Es werden die jeweils offenen Mengen vorgeschlagen.
Die Checkbox Erledigt wird automatisch vorbesetzt, wenn die insgesamt zugebuchte Menge der Soll-Losgröße entspricht. Ist ein Los vollständig erledigt, so können darauf keine Zeiten mehr gebucht werden. Wenn der Haken bei erledigt herausgenommen wird, so ist das Los im Status teilerledigt und kann daher noch bebucht werden.
Los erledigen
Da die manuelle Erledigung von Losen als Möglichkeit der Unterlieferung von Losen gedacht ist, werden bei der manuellen Erledigungsbuchung keine Abbuchungen vom Lager ins Los durchgeführt. Lediglich bei negativen Sollmengen, also geplanten Rückgaben aus dem Los ans Lager, werden Lagerzubuchungen dieser Mengen durchgeführt.
Wird der Erledigungsstatus eines Loses aufgehoben, so werden keinerlei Lagerbuchungen durchgeführt. Wenn ein Los manuell erledigt wird, werden alle Ablieferungen nachkalkuliert.
Automatisch erledigen
Insbesondere in Umgebungen mit Zeiterfassungsterminals ist der Wunsch, dass die Lose sich automatisch erledigen. Hierbei ist zu beachten, dass es in diesen Konstellationen auch immer wieder dazu kommt, dass offline Geräte, z.B. die Zeiterfassungsstifte, verwendet werden um effizient Zeiten erfassen zu können. Das bedeutet, dass zwar die Ablieferbuchung am Terminal gemacht wird und somit die gefertigte Stückzahl im Lager gebucht wird, aber, aufgrund der Offline Erfassung sind unter Umständen noch nicht alle Zeitbewegungsdaten eines Loses auf das Los gebucht. Würde nun das Los sofort abgeschlossen werden, würden die Zeiten und somit die Kosten fehlen und die Zeiten könnten nicht mehr nachträglich auf das vollständig erledigte Los gebucht werden.
Daher haben wir einen Automatik-Job geschaffen, der ein mal täglich (in der Nacht) prüft, ob Lose erledigt werden sollen / können. Wenn ein Los eine Abliefermenge hat, die gleich oder größer der Losgröße ist und wenn die letzte Ablieferbuchung länger als drei Tage (siehe Automatik im Modul System) vergangen ist, so wird versucht das Los automatisch zu erledigen. Kommt es bei der Erledigungsbuchung zu Fehlern, so wird in diesem Lauf das Los übersprungen. Am nächsten Tag / beim nächsten Lauf wird erneut versucht das Los zu erledigen. Wenn in der Zwischenzeit der Fehler verschwunden ist, wird das Los dann erledigt.
Wenn dieser Automatikjob aktiviert ist, sollte es keine alten nicht erledigten Lose geben. Bleiben Lose stecken, so prüfen Sie deren Erledigung manuell (Menü, Bearbeiten, Manuell Erledigen).
Dokumente zur Ablieferung
Wenn der Artikel eines Loses als Dokumentenpflichtig gekennzeichnet ist, so müssen nach einer erfolgten Ablieferung auch Dokumente zur jeweiligen Ablieferung hinterlegt werden. Ein Los, bei dem der Artikel als Dokumentenpflichtig gekennzeichnet ist, kann erst dann vollständig erledigt werden, wenn hinter jeder Ablieferungsbuchung ein entsprechendes Dokument hinterlegt ist.
Da Dokumentenpflichtig nur für Artikel hinterlegt werden kann, kann für die Ablieferung einer Materialliste kein Dokument hinterlegt werden.
Das Icon zur Dokumentenablage wird erst angezeigt, wenn es eine Ablieferungsbuchung gibt.
Kosten
Für die Berechnung der Material-Ablieferpreise werden immer die Gestehungspreise des auf das Los gebuchten Materials entsprechend seiner Zubuchung verwendet. Der kalkulatorische Preis (Kalk.Preis) aus der Stückliste hat KEINE Auswirkung auf die Werte der Ablieferung.
Für die Ermittlung der Personalkosten werden die auf das Los gebuchten Zeiten verwendet, wobei bei Teilablieferungen die Satzgrößen berücksichtigt wird. Während der Teilablieferungen werden die Zeiten der Arbeitsgänge anhand der Teilstunden, welche aus den Stunden pro Stück (Sollsatzgröße) errechnet werden, anteilig auf die Ablieferung angerechnet. Erst bei vollständiger Erledigung werden alle Stunden als auf dem Los verbraucht angenommen. Für die Maschinenzeitkosten wird im Sinne der Stundenanzahl in gleicher Weise vorgegangen. Als Basis für den Stundensatz der Mitarbeiter-Zeiten kommt der Parameter PERSONALKOSTEN_QUELLE zur Anwendung. Für die Maschinenstunden kommt der unter der jeweiligen Maschine zum jeweiligen Zeitpunkt gültige Stundensatz zur Anwendung.
Unterschiedliche Gestehungspreise
Bei jeder Losablieferung wird versucht, den Gestehungspreis, getrennt in Arbeit und Material, der abgelieferten Mengen möglichst exakt zu bestimmen. Bei Teilablieferungen ergibt sich hier, dass, eventuell nur teilweise, bereits mehr Material bzw. Arbeitszeit auf das Los gebucht ist, als tatsächlich für diese Teilablieferung benötigt wird. Daraus folgt, dass bei Teilablieferungen die Mengen immer nur bis zur sogenannten Sollsatzgröße berücksichtigt werden. Handelt es sich um Material, so kann, bei richtigen Stücklisten, die Sollsatzgröße nicht unterschritten werden, da ja damit eines der Geräte nicht vollständig wäre, handelt es sich um Arbeitszeit, so haben Ihre Mitarbeiter schneller als geplant gearbeitet. Werden nun Teilabgelieferte Lose vollständig erledigt, so werden auf die letzte Ablieferung alle verbleibenden Kosten aufgerechnet.
Beispiel: Die Losgröße ist 100 Stück, 98 Stück können sofort fertiggemeldet werden. Zwei Stück müssen überarbeitet werden. Nun wird die gesamte verbrauchte Mehrzeit und auch das zusätzlich verbrauchte Material auf die letzten zwei Stück der Ablieferung verteilt.
Stellt sich heraus, dass eine Unterlieferung stattfindet, weil z.B. ein Artikel nicht verwendet werden kann, so werden die gesamten Kosten auf das letzte Gerät verteilt.
Daraus können sich stark unterschiedliche Gestehungskosten je Ablieferung ergeben. Umgekehrt hat diese strenge Betrachtung den Vorteil, dass z.B. Anlaufkosten nur in den ersten Ablieferungen enthalten sind oder dass Sie sehen dass die eine Fertigungsschicht zu anderen Kosten arbeitet als die andere usw.
Da dies ohne die Stückrückmeldung die genauest mögliche Betrachtung ist, hängt die Richtigkeit der Teil-Ablieferungen von der Genauigkeit Ihrer Sollvorgaben ab. Werden, so wie in manchen Betrieb üblich, Sollzeiten von einer Minuten angegeben und am Schluss werden für fünf Stück (=Losgröße) 10 Stunden benötigt und es wird jedes Stück einzeln fertig gemeldet, so ergibt sich, da ja Aufgrund der Sollsatzgröße nur je eine Minute auf die ersten vier Lose gebucht werden darf, für die letzte Ablieferung ein Zeitaufwand von 295 Minuten.
Wenn der Parameter LOSABLIEFERUNG_GESAMTE_ISTZEITEN_ZAEHLEN gesetzt ist, so zählen für den Ablieferwert nur die Zeiten bis zum Abliefzeitpunkt. Das bedeutet, dass die erste Loasblieferung alle Zeiten bis zum ersten Ablieferzeitpunkt enthält und alle weiteren Ablieferungen jeweils die Zeiten ab dem vorherigen Ablieferzeitpunkt bis zum aktuellen Ablieferzeitpunkt beinhalten. Die letzte Ablieferung (Wenn das Los erledigt ist) enthält die Zeiten ab der vorletzten Ablieferung + Zukunft (= Nachträglich gebuchte Zeiten).
Zeitpunkt der Ablieferung
Um nun bei groben Buchungsfehlern, insbesondere im Sinne der richtigen zeitlichen Reihenfolge, trotzdem und nachträglich die richtigen Kosten den Losen und den damit verbundenen nachträglichen Belegen, z.B. Lieferschein, die richtigen Werte zur Verfügung stellen zu können, kann der Zeitpunkt der Losablieferungsbuchung gegebenenfalls manuell korrigiert werden.
Sie greifen damit in die zeitliche Abfolge der Zubuchung ein. Dies kann, insbesondere in der Gestehungspreisberechnung und im Sinne der Inventur entsprechende Auswirkungen haben. Ändern Sie diesen Zeitpunkt nur, wenn es unbedingt erforderlich ist.
Gestehungspreis nachträglich ändern
Manchmal ist es erforderlich, die errechneten Ablieferpreise eines Loses nachträglich zu verändern.
Stellen Sie die Ursachen richtig. Wenn Wareneinstandspreise falsch waren, korrigieren Sie den Wareneingang. Wenn Falsche Mitarbeiter- bzw. Maschinenzeiten gebucht wurden, korrigieren Sie die Zeiten.
Nach dieser Korrektur muss unter Umständen die Neukalkulation der Ablieferpreise angestoßen werden. Verwenden Sie dazu die Schaltfläche “Neu kalkulieren”.

Schaltfläche “Neu kalkulieren”
In einigen Fällen würde die Aufrollung der fehlerhaften Ursprungsdaten zu kompliziert werden. In diesen Fällen verwenden Sie bitte die manuelle Korrektur des Gestehungspreises im Modul Artikel, oberer Modulreiter Lager. Bitte beachten Sie, dass bei dieser Korrektur die Verkettung der Warenbewegungen gelöst werden muss und damit verloren geht.
Rücknahme der gesamten Losausgabebuchung
Ist ein Los noch nicht teilweise erledigt, so kann durch Klick auf Ändern in den Kopfdaten des Loses, der Status des Loses von ausgegeben / in Produktion auf angelegt zurückgenommen werden. Das bedeutet, dass der gesamte Inhalt der Materialbuchungen vom Los wieder an das Lager zurückgegeben wird.
Mehr produzieren als vorgesehen (überliefern)
Wenn Aufgrund der eingegebenen Gesamtmenge eine Überlieferung des Loses erfolgt, also mehr produziert wurde als in der Losgröße geplant war, so erhalten Sie eine Rückfrage.
Mit nein wird die Ablieferung abgebrochen.
Bei Ja wird die Überlieferung ohne Änderung der Los-Solldaten zugebucht. D.h. wenn Sie z.B. aus der Produktion eines Zuschnittsvorganges (z.B. werden von einer Stange Scheiben herunter geschnitten) mehr erhalten als errechnet, so ändert sich ja der Materialbedarf nicht, "nur" die erhaltene Stückzahl ist höher.
Bei Abliefern + Losgröße ändern, wird die Losgröße auf die neue Stückzahl erhöht und die Solldaten und die Materialentnahmen auf das Los werden auf die neue Losgröße angepasst.
Beachten Sie dazu die Einstellung Überlieferbar in den Kopfdaten der dazugehörenden Stückliste. Diese Einstellung der Stückliste dient nur der Steuerung der Überlieferung an den Zeiterfassungsterminals.
Meldung Sollsatzgröße unterschritten
Wenn eine Ablieferbuchung gemacht wird, so benötigen Sie, für jedes Stück welches produziert wurde, eine durch die Los-Sollmengen vorgegebene Anzahl / Menge an Material. Üblicherweise wird diese Menge durch die Stückliste vorgegeben. Wird nun eine Ablieferbuchung gemacht, so muss für die Anzahl der produzierten Artikel je Satz das Material im Los gebucht sein. Ist dieses Material nicht vorhanden, so kann das Produkt auch nicht erzeugt werden.
Wenn Sie Lose abliefern und bekommen die Meldung Sollsatzgröße unterschritten, so kann diese Meldung bei entsprechenden Rechten übersprungen werden. Wenn Sie dies machen, so müssen Sie sich bewusst sein, dass nun diese Mengen in der Mengen UND Kostenbetrachtung fehlen. Dies ist auch der Grund, warum z.B. Ablieferbuchungen am Terminal nur mit ausreichenden Mengen für die entsprechend abgelieferte Produktmenge gemacht werden dürfen.
Etikett drucken
Klicken bei der Ablieferung auf Etikette drucken. Im nun erscheinenden Druckdialog wird die Anzahl der Exemplare auf Basis der Abliefermenge durch die im Artikel eingepflegte Verpackungsmenge (Artikel, Sonstiges) errechnet. Ist hier keine Menge angegeben, so werden die Exemplare mit 1 vorbesetzt. Ein nicht passendes Ergebnis wird aufgerundet.
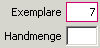
Istzeitdaten aus Soll übernehmen
Grundsätzlich empfehlen wir die exakte Istzeiterfassung, um eine exakte Nachkalkulation sicherzustellen. Gegebenenfalls kann es für Sie effizienter sein, die geplanten Sollzeiten als Istzeiten zu verwenden. Dafür verwenden Sie den Parameter ISTZEITEN_GLEICH_SOLLZEITEN.
Wird diese Funktion verwendet, so wird davon ausgegangen, dass die Sollzeiten des Arbeitsplanes (Reiter Zeitdaten im Los) auch als Ist-Zeiten verwendet werden. Für die im Los herangezogenen Ist-Zeiten werden die Sollzeiten des jeweiligen Arbeitsganges unter Berücksichtigung der abgelieferten Menge verwendet.
Beispiel: Geplante Rüstzeit 1 Stunde, geplante Stückzeit 10 Minuten, Losgröße 10 Stück. Es ergibt sich daraus eine Sollzeit von 2,67 Stunden.
Werden nun 8 Stück zurückgemeldet (Ablieferung) so wird eine Ist-Zeit von 2,67 / 10 * 8 Stunden = 2,14 Stunden gespeichert. Wird ein Los dann mit dieser Menge auf vollständig erledigt gesetzt, so bleibt wertmäßig das verbrauchte Material am Los und es wird nur die Ist-Zeit zur Basis der Ablieferung (also die 2,14 Stunden) verwendet.
Ablieferung mit Seriennummer
Für die Ablieferung können Sie die automatische Vergabe einer fortlaufenden Seriennummer einschalten. Beim Start des Seriennummern Erfassungsdialoges steht der Cursor im Seriennummern Feld. Drücken Sie nun Strg+O, um die nächste Seriennummer anhand der oben beschriebenen Seriennummernautomatik zu bekommen. Somit steht die nächste frei verfügbare Seriennummer im Seriennummern Erfassungsfeld.
Drücken Sie nun Enter und die Seriennummer wird in die darüber liegende Liste der erfassten Seriennummern übernommen. Nun drücken Sie erneut Strg+O und bekommen die nächste freie Seriennummer und drücken erneut Enter.
Links oben wird die abzuliefernde Menge angezeigt, rechts oben die bereits erfasste Anzahl der Seriennummern. So haben Sie jederzeit den Überblick, wie viele Seriennummern Sie bereits erfasst haben.
Ergänzend steht die Seriennummernerfassung mit Angabe der Stückzahl zur Verfügung. Das bedeutet, es wird die Startseriennummer, durch Klick auf oder Strg+O oder manueller Eingabe angegeben. Sie schalten durch entfernen des Hakens bei Komma auf Seriennummern von bis Eingabe um und stellen den Radiobutton auf Anzahl. Nun geben Sie unter Anzahl die gewünschte Stückzahl ein und klicken entweder auf Plus um die errechneten Seriennummern in der Auswahlliste zu sehen und eventuell noch zu bearbeiten, oder Sie klicken direkt auf Übernehmen womit die erzeugten Seriennummern in die davor liegende (Ablieferungs-) Erfassung übernommen werden.
Die Einstellung von Komma kann mit dem Parameter DEFAULT_SNR_DIALOG_KOMMA voreingestellt werden.
Der Vorschlagswert für das beginnt mit der Seriennummernreihe kann mit dem Parameter SERIENNUMMER_BEGINNT_MIT voreingestellt werden.
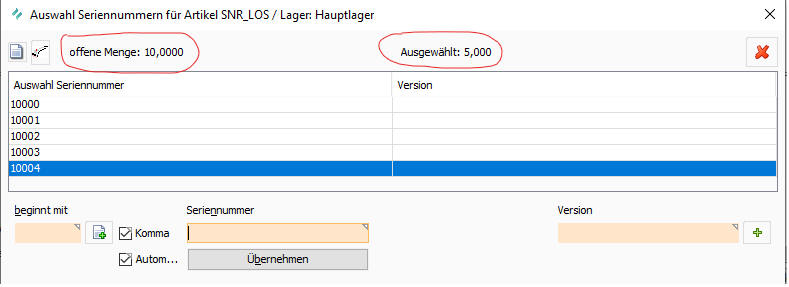
Vorgegebene Seriennummer
Es kommt immer wieder vor, dass auf Produkten bereits von anderen Systemen Seriennummern vorgegeben sind. Damit die Erfassung der Seriennummer und der Ablieferung nun auf schnelle Weise erfolgen kann, steht in der Ablieferung auch die Barcodeablieferung zur Verfügung. Bei dieser Art der Seriennummernerfassung wird auf die GS1 Codedefinition Bezug genommen.
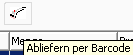
Seriennummer per Barcode scannen
Losklassen
Mit den Losklassen haben Sie die Möglichkeit, Fertigungslose für weitere Auswertungen zu markieren. Die Losklassen werden in der Fertigungsverwaltung → Grunddaten hinterlegt.
Die Losklassen sind unabhängig von dem Mandanten, alle angelegten Losklassen stehen für alle Mandanten zur Verfügung. Das hat den Vorteil, dass dadurch auch übergeordnete Auswertungen durchgeführt werden können (z.B. Managementstatus).
Nachkalkulation
Die Nachkalkulation ist eine Gegenüberstellung der Soll- und Ist-Arbeitszeiten in Stunden und Kosten, sowie der Material Ist- und Sollkosten des gewählten Loses.
Im Ausdruck der Nachkalkulation wird auch der Arbeitszeitfortschritt der Personal- und der Maschinenzeiten angezeigt, mit einem entsprechend farbigen Verlauf. Der Balken ist 200% (Ist/Soll) breit. Solange er unter 90% ist, ist er grün, dann wird er orange ab 100% hellrot und ab 110% rot.
Zusätzlich wird mit dem Haken neben der jeweiligen Tätigkeit angezeigt, dass alle Arbeitsgänge dieser Tätigkeit bereits als fertig eingetragen sind. Die Anzeige der Nachkalkulation kann auch von den Terminals aus aufgerufen werden, um den Mitarbeitern eine entsprechende Fortschrittsinformation zu vermitteln.
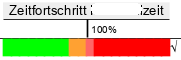
Zusatzstatus
Definition von Zusatzstatus
Sie können die Zuatzstatus im unteren Reiter Grunddaten → Zusatzstatus definieren.
Jedem Status kann ein Icon zugeordnet werden. Nachdem Sie die Zusatzstatus im Modul Fertigung definiert haben, sind diese auch in den allgemeinen Status eingetragen. Damit kann im System unterer Modulreiter Sprache, oberer Modulreiter Status dem neu angelegten Status auch ein entsprechendes Icon hinterlegt werden.
Erfassung von Zusatzstatus
In vielen Produktionsbetrieben ist die Erfassung eines des Fortschrittsstatus am einzelnen Fertigungsauftrag erwünscht. Üblicherweise wird dies Arbeitsplatzabhängig erfasst.
Daher steht in HELIUM 5 folgende Möglichkeit der Erfassung zusätzlicher Status im Fertigungsauftrag zur Verfügung. Falls Sie das Los bearbeiten wollen, muss jeweils der Zusatzstatus zurückgesetzt werden. Klicken Sie dazu auf Bearbeiten und beantworten Sie die Frage entsprechend und führen dieses Vorgehen bei Bedarf erneut durch.
Barcodescannern mit Wedge Interface kann durch eine spezielle Programmierung des Barcodeheaders und durch Scann der Losnummer des Fertigungsbegleitscheines der Status mittels Barcodescanner gesetzt werden. Die Funktion des Scannens des Zusatzstatus steht erst nach der Definition des Arbeitsplatzparameters und nach anschließendem Neustart des Fertigungsmoduls zur Verfügung. Dadurch wird erreicht, dass, sobald sich der Anwender in der Fertigungsauswahlliste befindet, kann direkt durch das Scannen der Losnummer vom Fertigungsbegleitschein der Status eingetragen werden. Wir haben dafür die Funktionstaste F12 verwendet. Nach drücken der F12, bzw. bei richtiger Einstellung des Wedge-CCD-Scanners erscheint ein Dialog zur Losnummer. Ist ein Status für ein Los schon eingetragen, erscheint ein entsprechender Hinweis. Ein eventuell falsch eingetragener Status muss unter dem oberen Modulreiter Zusatzstatus gelöscht werden.
Die Bedienung dieses Dialoges ist ausdrücklich für den Barcodescanner gedacht. Es können laufend die Lose gescannt werden. Zum Verlassen des Dialoges drücken Sie ESC oder klicken Sie auf das x rechts oben. Erscheint anstatt des obigen Dialoges so wurde eine falsche ID für den Arbeitsplatzparameter definiert.
Techniker
In den Kopfdaten des Loses kann der für das Fertigungslos verantwortliche Techniker definiert werden. Gegebenenfalls kann bei der Zeiterfassung die Auswahlliste auf die Techniker eingeschränkt werden.
Um weitere Techniker zu definieren, welche ebenfalls auf dieses Los buchen, wählen Sie den oberen Modulreiter Techniker. Definieren Sie hier die weiteren Personen, welche normalerweise ebenfalls auf dieses Los buchen dürfen.
Untere Modulreiter
offene AGs
Für die Planung und Steuerung der Fertigung ist das Wissen über die offenen Arbeitsgänge essentiell. Einen Überblick über alle offenen Arbeitsgänge aller Lose erhalten Sie im Modul Fertigung, im unteren Reiter Offene AGs (Arbeitsgänge). Um Informationen über spezielle Arbeitsgänge zu erhalten, nutzen Sie die Filtereingabemöglichkeiten und die Sortiermöglichkeiten der einzelnen Spalten. Mit dem GoTo-Button können Sie direkt zu dem ausgewählten Arbeitsgang wechseln.
In der Combobox werden nur die tatsächlich in dieser Liste vorhandenen Maschinen angezeigt. Maschinen, die als versteckt gekennzeichnet sind, aber trotzdem verwendet werden, werden mit einem führenden * gekennzeichnet, da diese Maschinen üblicherweise bereits ausgeschieden wurden.
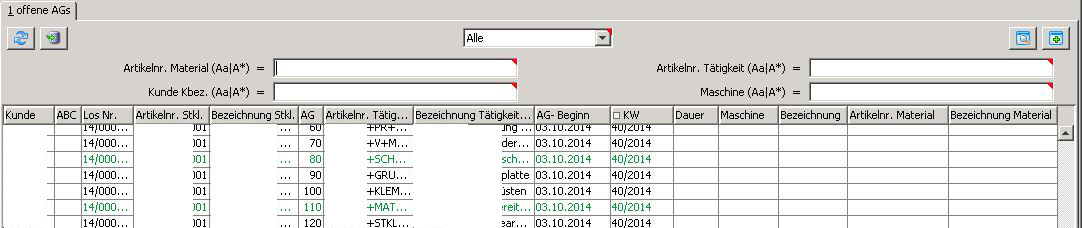
Arbeitsschritte steuern
Um die einzelnen Arbeitsschritte umzureihen, finden Sie im unteren Reiter Offene AG eine CheckBox Reihen. Wenn Sie hier einen Haken setzen, so ändert sich die Sortierung. Ab diesem Zeitpunkt erfolgt die Anordnung nach Maschine, AG-Beginn, Versatz-MS, Losnummer sortiert und es erscheinen die AUF/AB Pfeile.
Wenn Sie den aufwärtsgerichteten Pfeil anklicken, so wird zum Versatz 1ms hinzugefügt. Wenn Sie den aufwärtsgerichteten Pfeil anklicken, so wird zum Versatz 1ms abgezogen, solange bis Versatz-MS >=0 ist. Die Grenze für die Verschiebung ist der Kalendertag.
Zusätzlich gibt es in Verbindung mit der Zusatzfunktion Maschinenzeiterfassung den Reiter Reihen. Hier haben Sie die Möglichkeit, manuell die detaillierte Reihung der Arbeitsgänge / Lose vorzunehmen. Das bedeutet
Wählen Sie die gewünschte Maschine aus.
Klicken Sie nun auf "AGs anhand AG-Beginn sortieren". Damit wird anhand der aktuellen Reihenfolge der Arbeitsgang-Beginn-Datum in die interne Reihenfolgendefinition übernommen.
Nun kann geklickt werden. Es wird nun das I_REIHEN (je Maschine) berechnet (anhand der aktuellen Reihenfolge des AG-Beginns)
Nun kann mit Pfeilen sortiert werden. Diese Sortierung wirkt vor allem in Verbindung mit dem Erfassungsterminal.
einzelne Arbeitsgänge erledigen
Durch Klick auf Arbeitsgang Fertig(melden) kann dieser Arbeitsgang auf den Status Fertig gesetzt werden. Mit der damit verbundenen Aktualisierung der Liste verschwindet der Arbeitsgang damit zugleich aus der Auswahlliste und natürlich auch aus den offenen Arbeitsgängen in allen anderen Auswertungen.
Da es in der Praxis oft vorkommt, dass manche Arbeitsgänge von verschiedenen Menschen einfach nicht erfasst / übersprungen werden, kann durch Aktivierung des Parameters VORHERIGE_ARBEITSGAENGE_MITERLEDIGEN die Funktion zur Verfügung, dass damit beim Erledigen eines einzelnen Arbeitsganges alle davor noch nicht erledigten Arbeitsgänge mit erledigt werden. Da das enterledigen durch Positionierung des Cursors auf einen erledigten Arbeitsgang und erneuten den Klick auf den grünen Haken erfolgt, wird bei der Enterledigung, unabhängig vom Parameter VORHERIGE_ARBEITSGAENGE_MITERLEDIGEN nur der gewählte Arbeitsgang enterledigt. Der Parameter hat den Vorteil, dass damit implizit die Pflege der offenen Arbeitsgänge und damit die Auslastungsplanung besser wird.
Oberer Reiter Produzieren
Das Ziel dieser Darstellung ist, damit in einfacher Weise, bereits angelegte Lose so zu optimieren, dass mit der idealen Reihenfolge möglichst geringe Rüstzeiten erreicht werden und zugleich auch Termingerecht geliefert wird. Der erste Schritt ist hier sicherlich, dass man sich die zusammenpassenden Teile entsprechend sortiert, also z.B. Teile die auf der gleichen Maschine gemacht werden oder auch Teile die das gleiche Ausgangsmaterial haben usw..
Dann sortiert man diese z.B. nach AG-Beginn(-termin). In der rechten Spalte = heute produzierbar, wird angezeigt, ob für dieses Los, ausgehend vom im Moment verfügbaren Lagerstand, ausreichend Material vorhanden ist. Bitte beachten Sie, dass hier auch für Unterstücklisten nur die derzeit im Lager befindlichen Mengen berücksichtigt werden. Die Verbrauchsberechnung erfolgt in der Reihenfolge in der Sie im Moment die Liste sortiert haben. D.h. es wird zuerst das Material für das in der ersten Zeile befindliche Lose verbraucht. Das was davon übrig bleibt im Los der zweiten Zeile usw.. Ist für das jeweilige Lose theoretisch ausreichend Material vorhanden, so wird der Haken bei heute produzierbar angezeigt.
Durch das Verdichten fassen Sie mehrere Lose zusammen. Für die Verdichtung wird wie folgt vorgegangen:
Es werden nur Lose gleicher Stücklisten in sich zusammengefasst.
Es wird immer auf das vom Beginntermin älteste Los hin verdichtet.
Für dieses älteste Los wird die Losgröße so erhöht, dass damit die gesamte Losgröße der verdichteten Lose produziert wird.
Die nun überzählen Lose werden storniert.
Lose bei denen nachträgliche Materialentnahmen gebucht sind, werden beim Verdichten ausgelassen.
Da das Verdichten NUR für angelegte Lose möglich ist, werden in dieser Sicht nur Lose im Status angelegt angezeigt.
Sie haben die Möglichkeit, alle markierten Lose gemeinsam auszugeben. Sie werden der Reihenfolge nach von oben nach unten ausgegeben. Wird die Ausgabe bei einem Los abgebrochen, werden auch die nachfolgenden Lose nicht mehr ausgegeben. Da bereits ausgegebene Lose im Reiter Produzieren NICHT angezeigt werden, sehen Sie die durch den Abbruch noch nicht ausgegebenen Lose weiterhin in der Liste und können so komfortable diese weiter behandeln.
Bei der Ausgabe erscheint die Abfrage, wie bei den Ausgaben vorgegangen werden sollte. Nur produzierbare bezieht sich auf das von Los zu Los sich ändernde verfügbare Material (das in der Reihenfolge erste Los verbraucht das Material und dann kann das nachfolgende nur ausgegeben werden, wenn ausreichend verfügbar ist). Direkt drucken bedeutet, dass der Fertigungsschein jedes Loses ohne dem Umweg über die Druckvorschau erfolgt.
Interne Bestellung
Mit der internen Bestellung können Sie einen Produktionsvorschlag berechnen lassen. Information finden Sie im Kapitel Interne Bestellung.
Wiederholende
In einigen Fertigungsbetrieben ist es aus strukturellen Gründen nicht sinnvoll, jeden kleinen Fertigungsauftrag exakt mit seinen Istzeiten zu bebuchen. Hier hat sich bewährt, dass sogenannte Monatslose angelegt werden. Diese sind nach Baugruppen gruppiert. Dies ist für die Erfassung der Istzeiten hinreichend genau und reduziert die administrativen Zeiten auf ein erträgliches Maß. Wiederholende Lose werden in der Fertigung, unterer Modulreiter Wiederholende definiert.
Zum Anlegen der wiederholenden Lose klicken Sie im Menü auf Bearbeiten → Wiederholende Lose anlegen.
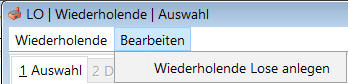
Feld | Bedeutung |
---|---|
Art | Artikel oder freie Materialliste |
Kostenstelle | Kostenstelle |
Stückliste | Artikelnummer des anzulegenden Loses |
Projekt | Projektbezeichnung. Hinweis dies wird um das Monat / die Zeitrauminformation ergänzt |
Ziellager | Ziellager der Zubuchung |
Fertigungsgruppe | Fertigungsgruppe |
Fertigungsort | Fertigungsort |
Wiederholungsintervall | In welchen Abständen sollte dieses Los angelegt werden |
ab | Ab welchem Stichtag wird das Los angelegt |
Losgröße | Mit welcher Losgröße sollte das Los angelegt werden |
Vorauseilend | Um wieviele Tage vor dem Stichtag sollte das Los vorher angelegt werden. |
Aktiv | Verwenden Sie diese Einstellung zum vorübergehenden deaktivieren der automatischen Anlage |
Sortierung | Reihenfolgedefinition |
Vorauseilend
Gegebenenfalls möchten Sie Ihre Monatslose immer um 5 Tage vor dem Monatswechsel anlegen, die Lose sollten entsprechend dem Stichtag einmal im Monat angelegt werden. Definieren Sie dafür, dass das Los zum 1. Los angelegt werden sollte. Durch das Wiederholungsintervall monatlich ist definiert, dass immer um ein Monat weiter gesprungen wird. Durch Vorauseilend z.B. 5 Tage definieren Sie, dass diese Prüfung bereits 5 Tage vorher erfolgt und somit zum 26.7. bereits das Los für den August angelegt wird.
Erledigen / Stornieren
Mit dem unteren Modulreiter Erledigen/Stornieren können mehrere Lose in einem Zug erledigt werden. Bei der Erledigung werden noch offenen Abliefermengen nachgebucht. In diesem Zuge werden auch Materialentnahmebuchungen aus dem Lager ins Los gemacht.
Um alle markierten Lose zu erledigen klicken Sie auf den grünen Haken. Weiters können Lose, die im Status angelegt sind, gemeinsam markiert und damit storniert werden. Sollten auch Lose markiert sein, die einen anderen Status als angelegt haben, werden diese nicht verändert.
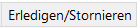
Rechte
Untere Modulreiter
Zusätzlich zum mindestens erforderlichen Leserecht für das Modul Los sind für die unteren Modulreiter folgende Rechte erforderlich:
offene Arbeitsgänge ... FERT_LOS_CUD und das Modul Zeiterfassung
Interne Bestellung ... FERT_LOS_CUD
Wiederholende ... FERT_LOS_CUD
Grunddaten ... LP_DARF_GRUNDDATEN_SEHEN
Das Recht FERT_LOS_CUD hat auch Auswirkungen darauf, welche Journale vom Benutzer aufgerufen werden können. Hat er dieses Recht, so stehen alle Menüeinträge für den Menüpunkt Journal zur Verfügung.
Hat er dieses Recht nicht, also z.B. nur FERT_LOS_R so werden im Menüpunkt Journal nur die Journale für Alle Lose, Offene Lose, Offene Arbeitsgänge angezeigt. Ab der Ablieferstatistik ist das schreibende Recht für die Lose erforderlich.
Ausgegebene Lose zurücknehmen
Es dürfen nur diejenigen Benutzer ein Los wieder in den Status angelegt zurücknehmen, die das Recht FERT_DARF_AUSGEGEBEN_ZURUECKNEHMEN besitzen. Dies ist vor allem dann von Bedeutung, wenn, z.B. Ersatztypen, Änderungen bei den Sollpositionen und oder den Ist-Mengen gemacht wurden.
Los erledigen
Um direkt im Reiter Ablieferung das Los auf erledigt zu setzen, ist das Recht FERT_DARF_LOS_ERLEDIGEN erforderlich.
Hat der Anwender dieses Recht nicht, so kann auch die manuelle Ablieferung aus dem Menüpunkt Bearbeiten, Manuell Erledigen nicht mehr aufgerufen werden.
Import
XLS Import für Lose
Sie finden den XLS Import für Lose im Modul Los → Menüpunkt Los → XLS-Import. Folgende Spalten können importiert werden.
Stückliste
Geben Sie die Artikelnummer der Stückliste an.
Projekt
Geben Sie die Projektbezeichnung an.
Losgroesse
Geben Sie die zu produzierende Menge an. Sollte die Menge 0 sein, wird die Zeile nicht importiert. Die Spalte der Losgröße muss als Zahl formatiert sein.
Endetermin
Geben Sie das Datum an, an dem die Produktion beendet sein soll. Der Beginntermin wird anhand der Durchlaufzeit der Stückliste errechnet. Die Spalte des Endetermins muss als Datum formatiert sein.
Kommentar
Tragen Sie einen Kommentar ein.
Damit der Pfad nicht jedes Mal neu eingestellt werden muss, haben wir dies so programmiert, dass nach der Auswahl der Importdatei der Pfad abgespeichert wird. Somit kann beim nächsten Import dieser Pfad wieder vorgeschlagen werden.
Solldaten importieren
Sie können Solldaten in freie Materiallisten importiert. Eine Musterdatei ist lossollmaterial.csv mit dem zweispaltigen Aufbau Artikel;Menge. Der Import wird gleich wie der Import des Ist-Materials über den CSV Import aufgerufen.
Je nach Status des Loses wird dies entsprechend importiert. D.h. ist das Los im Status angelegt, wird angenommen, dass dies Solldaten sind. Ist das Los im Status ausgegeben, wird dies als Materialverbrauch importiert.
Materialverbrauch importieren
Es gibt eine Möglichkeit zum Import von Materialverbrauch. Beim Import kann zwischen zwei Arten gewählt werden, und zwar “Echte Verbrauchsbuchung inkl. Chargen- bzw. Seriennummern” und “Harmonisierung von Lagerständen”. Für den Import klicken Sie im Reiter Material des Loses auf CSV-Import Istmaterial. Wählen Sie dann bitte die zu importierende Datei aus und beantworten die nachfolgende Frage entsprechend. D.h. damit wird entschieden welche Art von Daten Sie von z.B. Ihrem Bestückungsautomaten erhalten haben, womit sich zwei verschiedene Vorgehensweisen umsetzen lassen.
Echte Verbrauchsbuchung inkl. Chargen- bzw. Seriennummern
Die gesamten Bauteile werden faktisch im Bestückungsautomaten gelagert und Ihr Automat weiß immer nur "seinen" Lagerstand. Damit ist es auch erforderlich, dass Sie nach jedem Los die Daten aus dem Bestückungsautomaten exportieren und exakt in dieser Reihenfolge wieder in Ihr HELIUM V einlesen.
Harmonisierung von Lagerständen
Es werden vom Automaten die Verbrauche JE Bestückungsauftrag in die CSV-Datei gespeichert. Damit müssen diese Verbrauche (nur) passend zum jeweiligen Los eingelesen werden. Trotzdem ist bei eventuellen Chargen die richtige Reihenfolge des Einlesens für den passenden Verbrauch der Chargennummern (siehe unten) wichtig.
Das Dateiformat ist CSV mit Strichpunkt getrennt. Die Reihenfolge der Felder ist: Artikelnummer;Menge;SerienChargennummer. Als Dezimaltrenner wird der Punkt verwendet. Es wird kein Tausendertrenner verwenden.
Wird der resultierende Lagerstand eingelesen, so können keine Serien/Chargennummern übergeben werden. In diesem Falle wird immer die älteste Serien-/Chargennummer zuerst verbraucht. Wenn ein Artikel Seriennummer oder Chargennummern geführt ist und es wird eine Serien- bzw. Chargennummer übergeben, so wird automatisch der älteste Wareneingang mit dessen Serien-/Chargennummer verwendet.
Diese Funktion wird gerne für eine Harmonisierung mit einem externen Bestückungsautomaten mit oder ohne eigener Lagerwirtschaft verwendet. D.h. wenn je gefertigtem Los der Lagerstand harmonisiert wird, ist die Differenz die Menge die vom Automaten verwendet wurde. Damit sind auch die, gerade bei SMD Automaten oft verworfenen Bauteile, welche einen Mehrverbrauch darstellen, darin enthalten.
Bitte beachten Sie, dass beim Import der verbrauchten Menge diese immer dazugebucht wird. Beim Import des resultierenden Lagerstandes wird immer die Differenz zwischen dem Lagerstand in HELIUM 5 und der übergebenen Liste in das jeweilige Los gebucht. Beachten Sie dies bei der Ausgabe des Loses. Wird der reine Verbrauch eingelesen, so darf vorher bei der Losausgabe KEIN Material gebucht werden. Wird der Lagerstand eingelesen und damit nur die Differenz gebucht, so kann die Materialentnahme in HELIUM 5 durchaus auch mit der Ausgabe mit gebucht werden (Standardeinstellung) und es wird nur die Differenz gebucht.
Der Zweck dieser Funktion ist, dass Ihr ERP System immer das führende System sein muss und dadurch jeder Benutzer z.B. der Einkauf, jederzeit über den richtigen Lagerstand informiert ist.
Traceimport
Eine weitere Möglichkeit ist einen sogenannten Tracereport, also eine Aufstellung welche Chargen / Batch-ID für welche Stücklisten verbraucht wurden einzuspielen und so die oft umfangreiche Chargenerfassung deutlich zu vereinfachen. Sie finden diesen Import im Modul Los, Menüpunkt Los, Import, TraceImport.
Da, gerade bei SMD, die Fertigung / Bestückung oft in mehreren Durchläufen erfolgen muss, denken Sie an SMD Oberseite / Unterseite, ist der Import immer additiv, also hinzufügend. Eine Musterdatei finden Sie im Musterdateiverzeichnis unter TraceReport_Muster.txt. Der Aufbau ist Text, Tabs getrennt.
Die wesentlichen Informationen werden aus der ersten Spalte (Layout) und aus der 10. Spalte (Batch) verwendet. Zusätzlich können zwei Arten von Traceimport-Formaten unterschieden werden. Die Tracedatei der My9 hat 13 Spalten. In der Spalte 10 ist der Batch, welcher von HELIUM 5 als Chargennummer eingelesen wird, enthalten. Die Tracedatei der My200 hat 14 Spalten. Hier findet sich der Batch, also die Chargennummer in der Spalte 11. In der Spalte 1 = Layout steht die Artikelkurzbezeichnung der Stückliste. Diese wird noch um die Definition ergänzt, dass nur die Zeichen bis zum ersten / Schrägstrich (ohne demselben) verwendet werden. Die Spalte Batch entspricht der verwendeten Chargennummer. Die Spalte 5 = PCB-Nummer liefert die laufende Leiterplatten-Nummer auf die die Bauteile bestückt wurden.
Jede Zeile des Tracefiles repräsentiert 1 Stück Verbrauch der jeweiligen Chargennummer im gefundenen Los. Beispiel für die Spalte Layout: Im Tracefile steht: 358417-297113/SE171208Co. Es wird eine Stückliste mit der Kurzbezeichnung 358417-297113 gesucht. Für die Materialbuchung muss das Los im Status In Produktion bzw. teilerledigt sein.
Trennung Ober / Unterseite erfolgt dadurch, dass "nur" das erhaltene Material verbucht wird. Damit werden die verschiedenen Materialverbrauche eingebucht. D.h. wenn später noch was nachbestückt wird, kann man das auch einspielen.
Ablauf des Imports: Starten Sie den Importvorgang und wählen Sie die entsprechende Datei aus. Nun klicken Sie auf aktualisieren. Hier erhalten Sie eine Anzeige über die fehlerhaften Einträge in dieser Tracedatei in Bezug auf die in Ihren, im Status ausgegebenen, in Produktion oder teilerledigt befindlichen Lose. Zeilen ohne Fehler werden in dieser Vorabprüfung nicht angezeigt. Geprüft wird, ob der anhand der Charge ermittelte Artikel in einem der Lose benötigt wird. Entspricht der Import Ihren Vorstellungen, so klicken Sie auf Import durchführen. Es werden nun die ermittelten Bauteile den Los-Soll-Materialpositionen zugewiesen und dies in einer Buchungsliste angezeigt.
Die Stückliste ist die Artikelnummer der Stückliste des Loses.
Das Material ist die Artikelnummer des zu buchenden Materials.
Die Bezeichnung ist die Bezeichnung des Artikels des Materials.
Die Charge ist die verwendete Chargennummer.
PCB ist die Anzahl der Leiterplatten, die mit dieser Menge bestückt werden konnten.
Der Lagerstand ist der Lagerstand der Charge.
Offen ist die Menge, die noch in das Los gebucht werden soll.
zu Buchen ist die Aufgrund des Traceimportfiles zu buchende Menge der Charge auf die jeweilige Losposition ausgehend von der Originalposition.
Insbesondere wenn mehrere Baugruppen in diesem Tracefile enthalten sind, z.B. die Produktion eines ganzen Tages, können die Zuordnungen entsprechend unterschiedlich ausfallen. D.h. gegebenenfalls korrigieren Sie die zu buchende Menge. Hier ist es auch erlaubt, eine größere Stückzahl als tatsächlich laut Berechnung offen ist einzugeben. Beachten Sie jedoch, dass keine wie immer gearteten Übertragsberechnungen bzw. Korrekturen durchgeführt werden. D.h. wenn von Ihnen Mengen korrigiert / umgebucht werden, so müssen diese in sich stimmig sein.
In Verbindung mit der Ersatztypen-Verwaltung, werden für das Feld "zu Buchen" die hinterlegten Ersatztypen mit berücksichtigt. Das bewirkt, dass die Sollmengen des Originalartikels als auch die Sollmengen der dem Originalartikel zugeordneten Ersatztypen zusammengezählt werden. Der Verbrauch, durch die Chargen (Artikel) wird dann von oben nach unten den jeweiligen Losen / Lospositionen zugewiesen. Damit wird erreicht, dass bei der Bestückung sehr flexibel die vom Automaten verwendeten Chargen, egal ob diese auf die Originalartikel oder die Ersatzartikel zeigen, vorgegangen werden kann. Zusätzlich werden die Verbrauche nach Losnummern aufsteigend sortiert. D.h. die Lose mit den niedrigeren Nummern werden zuerst aufgefüllt.
Wurden die Mengen geprüft und für gut befunden, klicken Sie auf durchführen (grüner Haken), womit die Materialbuchungen vom Lager ins Los tatsächlich durchgeführt werden. Eine Verriegelung der importierten Datei erfolgt nicht, da diese meist auch noch von anderen Systemen verwendet wird. Am Ende des Importes wird die importierte Datei um _importiert ergänzt. Damit ist ersichtlich, dass diese Datei schon einmal importiert wurde.
Bitte achten Sie darauf, die gleiche Datei nicht mehrfach zu importieren.
Mögliche Fehlermeldungen des Traceimports:
Es wurde keine Stückliste der Kurzbezeichnung 358417-297113 gefunden. Bitte stellen Sie die Definition der Kurzbezeichnung Ihrer Stücklisten richtig.
Es konnte kein Artikel der Chargennummer R123456 gefunden werden. Es gibt keinen lagernden Artikel dieser Chargennummer.
Es konnte kein Los im Status, ausgegeben/In Produktion/Teilerledigt gefunden werden. Bedeutet: Es wurde ein passender Artikel für die erhaltene Chargennummer gefunden. Es konnte aber kein Los der Stückliste gefunden werden, in dem dieser Artikel noch Fehlmenge ist
Für den Traceimport ist nur die Chargennummer relevant. Die für die Chargennummer auch zur Verfügung stehende Version, welche in manchen Installationen anders verwendet wird, wird bei der Ermittlung des verfügbaren Lagerstandes dieser Chargennummer nicht berücksichtigt.