Besondere Sachlagen und Tipps für Lose
Gewichtswarnung
Gegebenenfalls benötigen Sie einen Hinweis, wenn die Summe der Materialgewichte einen Grenzwert überschreitet. Verwenden Sie dafür den Parameter GEWICHTSHINWEIS. Als Gewichtsgrenze dient das im Mandantenparameter GEWICHTSHINWEIS angegebene Gewicht in kg. Diese Info wird nur bei der Neuanlage eines Loses ausgegeben.
Materialausgabe ist erste Tätigkeit
Gegebenenfalls ist bei Ihnen die Materialausgabe die erste Tätigkeit. Es stehen dafür zwei Parameter zur Verfügung.
MATERIAL_BEI_ERSTEM_AG_NACHBUCHEN
Ist der Parameter MATERIAL_BEI_ERSTEM_AG_NACHBUCHEN aktiviert, so wird beim Starten des Loses kein Material ausgegeben. Das verfügbare Material wird ausgegeben, sobald die erste Tätigkeit gebucht wird.
MATERIAL_ANHAND_GLEICHER_ARTIKELGRUPPE_BUCHEN
Ist der Parameter MATERIAL_ANHAND_GLEICHER_ARTIKELGRUPPE_BUCHEN aktiviert, so wird beim Starten des Loses kein Material ausgegeben. Das verfügbare Material mit derselben Artikelgruppe wie die Artikelgruppe des Arbeitszeitartikels der ersten Tätigkeit wird ausgegeben, sobald die erste Tätigkeit gebucht wird.
Beispiel: Sie produzieren Schränke und benötigen Bolzen. Es gibt eine Tätigkeit “Bolzen setzen”, bei der die Bolzen eingesetzt werden. Die Tätigkeit und die Bolzen haben dieselbe Artikelgruppe.
Weil MATERIAL_ANHAND_GLEICHER_ARTIKELGRUPPE_BUCHEN aktiviert ist, werden die Bolzen erst aus dem Lager ins Los gebucht, wenn die Tätigkeit “Bolzen setzen” erfasst wird.
Wird die Tätigkeit gelöscht, verbleibt das Material jedoch im Los.
Beide Parameter deaktiviert
Sind MATERIAL_BEI_ERSTEM_AG_NACHBUCHEN und MATERIAL_ANHAND_GLEICHER_ARTIKELGRUPPE_BUCHEN deaktiviert (= 0), so wird die übliche Materialbuchung anhand der anderen Parameter vorgenommen. Hier greifen vor allem auch die Stücklisteneigenschaft Materialbuchung bei Ablieferung bzw. die Parameter KEINE_AUTOMATISCHE_MATERIALBUCHUNG, BEI_LOS_ERLEDIGEN_MATERIAL_NACHBUCHEN.
Materialbedarf anhand der Arbeitspläne steuern
Mit dem Parameter AUTOMATISCHE_ERMITTLUNG_BEGINNTERMINOFFSET kann bei der Terminberechnung der Arbeitsgänge aktiviert werden, dass der Beginnterminoffset der Materialpositionen passend zum Arbeitsgangbeginn gesetzt wird. D.h. abweichend vom Beginntermin des Loses, werden die Artikel um den Arbeitsgangbeginn später benötigt. Somit scheinen diese Artikel entsprechend später im Bestellvorschlag bzw. in der internen Bestellung auf. Das reduziert Ihr Lager entsprechend.
Die Verbindung zwischen Tätigkeit und Material wird über die Artikelgruppen hergestellt. D.h. die früheste Tätigkeit einer Artikelgruppe definiert mit ihrem Arbeitsgangbeginn auch den Beginnterminoffset der Artikel der gleichen Artikelgruppe. Damit ist auch gegeben, dass wenn es für Artikel keine Artikelgruppen gibt, bzw. keine Tätigkeiten für diese Artikelgruppe definiert ist, so werden diese zum Beginntermin des Loses benötigt.
Lagerplatzzuordnung am Los
Mit der Zusatzfunktion LAGERPLATZ_IM_LOS kann im Los, durch Klick auf den Button jedem Los ein Lagerplatz, unabhängig vom Ziellager des Loses, zugeordnet werden. Ist die Zusatzfunktion aktiviert, so wird der Lagerplatz auch in der Losauswahlliste mit angezeigt.
Einmalige Ausnahme für einen Ersatzartikel
Bei aktiver Ersatztypenverwaltung ergibt sich immer wieder auch die Forderung, dass ausnahmsweise für dieses eine Los, ein weiterer Ersatzartikel zu einem Originalartikel hinzugefügt werden muss. Insbesondere in der Verbindung mit dem Traceimport, aber auch generell für die Betrachtung der Gegenüberstellung der Sollmengen mit den ausgegebenen Mengen, muss eine neue Los-Materialposition als Ersatztype für die Originalposition gekennzeichnet werden.
Um eine zusätzliche Position als Ersatztype zu definieren, gehen Sie bitte wie folgt vor
Fügen Sie den zusätzlichen Artikel über eine nachträgliche Materialentnahme bzw. eine neue Sollposition hinzu
Markieren Sie den Artikel und klicken Sie auf Als Ersatztype definieren.
Nun wählen Sie aus den aufgelisteten Original Sollpositionen diejenige Position aus, für die diese Position ein Ersatztype sein sollte. Somit ändert sich die Zeile auf grün und Sie erhalten, also N für Nachträglich hinzugefügt und grün für Ersatztype.
Mitwachsende Stücklisten
Gegebenenfalls erfassen Sie nur die wichtigsten Komponenten und eine grobe Schätzung für den tatsächlichen Materialbedarf in der Stückliste. Die tatsächliche Menge ergibt sich während der Produktion.
Da es meistens erwünscht ist, dass diese nachträglichen Änderungen ersichtlich sind, oft auch kein Bezug zu Sollpositionen herstellbar ist, verwenden Sie dafür die Funktion Nachträgliche Materialentnahme ohne Sollposition. Diese Zeilen werden durch die N (Buchungsart nachträglich) in den Materialpositionen angezeigt.
Werden zusätzliche Positionen benötigt, welche nicht auf Lager sind, so tragen Sie diese mit Neu ein. Bei einem Los In Produktion werden die Fehlmengen dadurch entsprechend aktualisiert, was wiederum zur Berücksichtigung im Bestellvorschlag führt. Da auch dies eine Änderung der Solldaten gegenüber der Stückliste ist, wird die Buchungsart ebenfalls auf Nachträglich gesetzt.
Sollte sich eine Materialentnahme auf eine Sollposition beziehen, so verwenden Sie dafür Nachträgliche Materialentnahme. Diese Buchung, wird bei einem Ausgegebenen Los ebenfalls zusätzlich in die Materialpositionen eingefügt, da sie aber einen Bezug zur Sollposition hat, wird als Buchungsart S(ollposition) angezeigt.
Abhängig von Fehlmenge reduzieren
Wird Fehlmenge reduzieren angehakt, so wird diese Buchung als die verspätete Entnahme auf die Sollposition betrachtet, die Fehlmenge reduziert und in den Losmaterialpositionen keine weitere Zeile mehr eingefügt. Auch wenn eine Entnahme durchgeführt wird, die größer als die tatsächliche Fehlmenge ist, wird dies als Entnahme mit direktem Bezug auf die Sollposition betrachtet.
Wird Fehlmenge reduzieren nicht angehakt bzw. abgehakt, so wird dies als zusätzliche Materialentnahme betrachtet und die Buchung ohne Sollmenge, aber mit Bezug auf die Sollposition eingetragen.
Material vorzeitig bestellen
Gegebenenfalls benötigen die Konstruktion, die Entwicklung und das Design eines neuen Produktes viel Zeit und Sie möchten die Bestellung der Komponenten beginnen, bevor diese abgeschlossen sind. Verwenden Sie dafür die mitwachsenden Stücklisten. D.h. die Stücklisten ändern sich während des Konstruktionsprozesses solange, bis sie den Vorgaben entsprechen. Es werden aber die Teile / Baugruppen die bereits bekannt sind, zum frühestmöglichen Zeitpunkt in die Stücklisten eingetragen. Somit können daraus Lose angelegt werden und der Bestellprozess gestartet werden.
Ein Beispiel:
Ein Kunde erteilt einen Auftrag.
Die Konstruktion, die Entwicklungsabteilung beginnt zu entwickeln, Dauer ca. 3 Wochen.
Die entwickelten Stücklisten werden aus der CAD der Konstruktion nach HELIUM 5 übernommen, die Lose angelegt, der Bestellvorschlag durchgeführt und die Bestellung an die Lieferanten übermittelt.
Die Beschaffung der teilweise auftragsspezifischen Teile dauert zwei Wochen.
Nun kann mit der eigentlichen Fertigung begonnen werden, diese dauert sechs Wochen.
Ergibt also insgesamt 11 oder 13 Wochen oder mehr.
Gelingt es nun, die Verteilung so zu machen, dass die Zukaufteile bereits bei Auftragserteilung bekannt sind, so kann eine vorab Stückliste angelegt werden und so der Beschaffungsvorgang um drei Wochen früher gestartet werden.
Das funktioniert, da bereits in der Angebotsphase ein Konzept vorliegt, welche Teile benötigt werden um den Auftrag erfüllen zu können. D.h. die wesentliches Einkaufskomponenten sind bekannt.
Gehen Sie wie folgt vor:
Kunde erteilt Auftrag
Konstruktion erstellt eine vorab Stückliste in der die wichtigen Komponenten enthalten sind. Dauer: 1/2 Tag
Die vorab Stückliste wird nach HELIUM 5 übernommen, die Lose angelegt, der Bestellvorschlag durchgeführt und die Bestellung an die Lieferanten übermittelt.
Die Beschaffung der Teile dauert 2-4 Wochen, während dessen konstruiert die Konstruktion weiter.
Die nun fertigen Stücklisten werden aus der CAD nach HELIUM 5 übernommen und die Lose aktualisiert.
Nun wird erneut ein Bestellvorschlag durchgeführt und eventuell noch fehlende Artikel werden nachbestellt.Damit kann die Fertigung um 2,5 bis 3 Wochen früher beginnen und ist innerhalb der Fertigungszeit von 6-7 Wochen am Ziel.
Nachteil: Es könnte sein, dass Sie in der Phase der Vorabstückliste falsche Artikel spezifizieren.
Besonderheiten in der Kunststofffertigung
In der Kunststofffertigung hat sich folgende Herangehensweise herausgebildet.
Ausschussmengen / Überproduktion
Üblicherweise werden ausgehend von der vom Kunden gewünschten Stückzahl eine Übermenge produziert um mit großer Wahrscheinlich die gewünschte Stückzahl zu erreichen. Dies wird üblicherweise durch die Erhöhung der Losgröße gegenüber der Auftragsmenge um den Ausschussfaktor vorgenommen. Sind in den Stücklisten auch Verpackungen enthalten, so sind diese von der Erhöhung ebenfalls betroffen.
Rückmelden der tatsächlich gefertigten/gespritzen Stückzahlen
Oft wird nicht nur die benötigte Stückzahl gefertigt sondern das Granulat vollständig verbraucht, da ja der Kunde in der Zukunft sicher wieder Teile benötigt. Es ist daher nach dem Spritzen der Teile die Losgröße auf die tatsächlich gefertigte Menge zu korrigieren (Siehe Los, Bearbeiten, Losgröße ändern). Damit wird das benötigte / verbrauchte Material entsprechend korrigiert.
Erfassung der tatsächlich verwendbaren Stückzahlen nach der Qualitätsprüfung.
Bei der Prüfung der Teile werden Teile aussortiert werden müssen, welche nicht den Vorgaben entsprechen. Dadurch werden zum Schluss weniger Teile abgeliefert als produziert wurden. Setzen Sie hier bei der letzten Buchung der Losablieferung den Haken bei Vollständig erledigt, so werden die Material- und Arbeitszeit-Kosten auf die reduzierte Ablieferungsgesamtmenge umgerechnet, da der Mehraufwand sich ja auf die Gutteile verteilen muss.
Ermittlung der Schusszahlen am Werkzeug
Diese kann aus der Statistik des Werkzeugs ermittelt werden. Dafür werden neben den verwendeten Losen auch die Erfassungsfaktoren (Schusszahl) benötigt. Ihre Formulare müssen entsprechend angepasst werden.
Rankingliste
Die Rankingliste dient der vollautomatischen Steuerung der Dringlichkeit der zu fertigenden Lose, gegliedert nach Fertigungsgruppe. Ziel: Liste mit dem Ranking der Fertigungsaufträge sortiert nach Fertigungsgruppe und darin nach Termin.
Ausgangspunkt ist die Reservierungsliste, also alle reservierten Stücklisten. Als erstes werden die Lagerstände in der Reservierungsliste verbraucht. D.h. was von den Reservierungen vom Lager bedient werden kann, braucht nicht gefertigt werden. Wenn es kein ausgegebenes Los in der Fertigung der Artikel gibt, so wird der Artikel nicht weiter berücksichtigt. Hintergrund: Der Mensch entscheidet ob der Fertigungsbeginn sinnvoll ist oder nicht.
Es dürfen hier NUR bereits ausgegebene Lose berücksichtigt werden.
Ein Los darf nur EINMAL aufscheinen.
Von welcher Fertigungsgruppe wird dieser Artikel gefertigt? Liste je Fertigungsgruppe (Seitenumbruch dazwischen) erstellen, sortiert nach Termin und Soll-Fertigungszeit (Dauer) absteigend.
Spezialfall Kabelschneider: Die Kabelschneider müssen jedes Los teilfertigen, da ja zuerst die Kabel vorbereitet = geschnitten werden müssen. D.h. grundsätzlich müssen die Kabelschneider alle Lose fertigen, mit Ausnahme derer, die sie bereits gefertigt haben. Dieser Produktionsschritt wird bereits durch den Zusatzstatus, Kabel Geschnitten erfasst.
Unterstücklisten
Hier gehen wir davon aus, dass diese terminlich vor den zu fertigenden Stücklisten eingeplant sind und damit automatisch rechtzeitig erscheinen. Sie werden also nicht extra berücksichtigt, sondern eben nur über die Reservierungen. D.h. das auch die Reservierungen der Lose mit eingehen.
Um die Listen kurz zu halten, werden nur die Lose, welche die nächsten 14 Tage zu fertigen sind angedruckt.
Moisture Sensitivity Level (MSL) Anforderungen
Gegebenenfalls möchten Sie Moisture Sensitivity Level abbilden. Hier geht es darum, dass aus Gründen der Fertigungsqualität die Elektronikbauteile nur eine kurze Zeit in freier Luft (Floor Life) sein dürfen. Hier werden 9 Stufen unterschieden, die je nach geforderter Qualität bei den Bauteilen zu beachten sind.
Stufe | Zeit | Bedingung |
---|---|---|
1 | unbegrenzt | 30 °C / 85 % RH |
2 | 1 Jahr | 30 °C / 60 % RH |
2a | 4 Wochen | 30 °C / 60 % RH |
3 | 168 Stunden | 30 °C / 60 % RH |
4 | 72 Stunden | 30 °C / 60 % RH |
5 | 48 Stunden | 30 °C / 60 % RH |
5a | 24 Stunden | 30 °C / 60 % RH |
Da in aller Regel dies selten und nur für sehr wenige Bauteile zur Anwendung kommt, empfehlen wir folgende Vorgehensweise vor
Lassen Sie die Definition für Farbcode in Artikel → Technik auf MSL ändern.
Tragen Sie die Stufen und deren Dauer in den Grunddaten des Artikels im Reiter MSL ein.
Definieren Sie nun die MSL sensitiven Artikel im Reiter Technik des jeweiligen Artikels.
Sie bekommen nun bereits in der Losausgabeliste die entsprechenden MSL Codes angedruckt, womit die Behandlung der Artikel definiert ist
Bei der Entnahme der Artikel aus dem Feuchteschutzbeutel / -bereich beginnt die Floor Life Time zu laufen. D.h. drucken Sie nun ein Artikeletikett, zum Beispiel ein Losentnahme-Etikett aus, auf dem das aktuelle Datum und Uhrzeit und der MSL aufgedruckt sind. Kleben Sie dieses Etikett auf die Bauteil-Verpackung.
Wenn das Bauteil wieder in den Feuchteschutzbereich eingelagert wird, drucken Sie erneut ein Artikeletikett mit aktuellem Datum und Uhrzeit, womit die sich nun ergebende Floor Life Time definiert ist.
Die Etiketten müssen angepasst werden. Bei Bedarf ist eine Spalte für den händischen Eintrag der gesamten Floor Life Time vorgesehen. Sie können somit sehr rasch erkennen, wann das Bauteil das nächste Mal ausgebacken (getrocknet) werden muss.
Ev. sollte für diese Bauteile auch die Reel-ID verwendet werden, womit eine Vereinzelung der jeweiligen Rollen gegeben ist.

Material des Kunden (Beistellware) bearbeiten
Gegebenenfalls erhalten Sie Beistellware von Ihren Kunden zur Verfügung gestellt, welche dann über kundenspezifische Stücklisten bzw. Lose verarbeitet werden. Sie möchten jederzeit wissen, wieviel vom Kundenmaterial noch da ist.
Lagern Sie die vom Kunden erhaltene Ware in ein Kunden-Lager ein. Dieses Lager ist üblicherweise als Konsignationslager gekennzeichnet. Im Los stellen Sie im Reiter Läger ein, von welchem Lager sich dieses Los bedienen darf. Stellen Sie ein, dass das Los nur vom Kunden-Lager abbuchen darf. Somit ist der entsprechende Verbrauch auf die Kunden-Stücklisten-Artikel dokumentiert. Zugleich ist der Lagerstand Ihrer Artikel auch für Ihren Kunden transparent nachvollziehbar.
Idealerweise definieren Sie in den Artikeln, die von Ihrem Kunden beigestellt werden, den Kunden auch als Lieferanten, aber zum 0,00 Null Preis. D.h. über den Bestellvorschlag werden die Artikel vom Kunden abgerufen, mit allen Möglichkeiten des Bestellungsmodules.
Es werden automatisch die Artikel, die von Kundenkonsignationslagern abgebucht werden, mit einem Gestehungspreis von 0,00 in die Lose gebucht. Dies hat vor allem dann eine Bedeutung, wenn Sie für Zoll- oder Versicherungszwecke trotz allem den auf den Kundenkonsignationslager eingelagerten Artikeln einen entsprechenden Wert geben müssen.
Manuelle Stückrückmeldung
Es steht die Manuelle Stückrückmeldung im Modul Los zur Verfügung. Die Idee dahinter ist, dass nur durch Scannen der Losnummer möglichst einfach die offenen Arbeitsgänge der Reihe nach gebucht bzw. erledigt werden können. Voraussetzung für die einfache Bedienung ist, dass auf dem erfassenden Rechner ein Barcodescanner zum Lesen der Los-Barcodes und der Personal-Barcodes mit einem sogenannten Wedgeinterface installiert ist.
Sie finden im Modul Los, Menü, Bearbeiten, manuelle Stückrückmeldung. Mit Aufruf dies Menüpunktes erscheint der Erfassungsdialog.
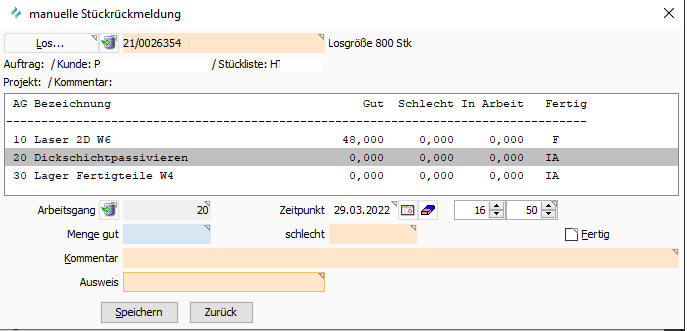
Erfassungsdialog Stückrückmeldung
Folgen Sie folgendem Ablauf:
Scannen Sie die Losnummer. Dadurch werden alle Arbeitsgänge des Loses angezeigt. Die Erfassungszeile steht auf dem ersten noch nicht erledigten Arbeitsgang. Erledigt bedeutet, dass bei diesem Arbeitsgang Fertig angehakt sein muss.
Für den ersten noch nicht erledigten Arbeitsgang steht der Cursor / die Erfassung im Feld Menge gut. Geben Sie die Gut-Menge ein und drücken Sie Enter.
Der Cursor steht im Feld Kommentar. Hier stehen nun zwei Möglichkeiten der Erfassung zur Verfügung.
Es wird der Barcode des Mitarbeiters, der diesen Arbeitsgang gemacht hat, gescannt. Dadurch erscheint dieser unter Ausweis bzw. rechts daneben der Name des Mitarbeiters.
Es wird ein Kommentar zu diesem Arbeitsgang eingegeben und anschließend TAB gedrückt, womit der Cursor im Feld Ausweis steht und so auch hier der Barcode des Mitarbeiters erfasst werden kann.
Wird von der Gut-Menge ausgehen TAB gedrückt, steht der Cursor im Feld Schlecht, in dem die Schlecht-Menge erfasst werden kann.
Mit einem weiteren TAB steht der Cursor auf Fertig, wo durch drücken der Leertaste dieses Feld aktiviert werden kann. Alternativ kann Alt+F gedrückt werden, wodurch sofort das Feld aktiviert ist. Mit einem erneuten TAB sind Sie wiederum im Feld zur Erfassung der Ausweisnummer / der Person die diesen Arbeitsschritt ausgeführt hat.
Nach dem Scannen der Ausweisnummer ist der Knopf Speichern aktiviert. Durch Enter, Alt+S, oder Klick auf den Button, wird die Erfassung abgespeichert.
Nun wird entweder
Die Erfassung mit dem nächsten Arbeitsgang fortgesetzt, indem mit der Maus der Cursor auf den nächsten Arbeitsgang gestellt wird oder
durch Klick auf Zurück die Erfassung beendet oder
mit Alt+L ein anderes Los ausgewählt oder
da der Cursor automatisch im Los Erfassungsfeld ist, kann mit einem Scann eine neue Losnummer eingescannt werden, womit die Erfassung für das nun gescannte Los beginnt.
Um Details zu den Stückrückmeldungen des Arbeitsgangs einzusehen, klicken Sie neben dem Arbeitsgang auf den GoTo Button , wodurch im Hintergrund die Anzeige der Stückrückmeldungen auf diesem Arbeitsgang angezeigt werden. Legen Sie einfach die Fenster entsprechend nebeneinander.

Als Ergänzung der Stückrückmeldung (Gut-/Schlecht-Stück) kann je rückgemeldeter Stückzahl gegebenenfalls auch noch ein entsprechender Fehler mit angegeben werden.
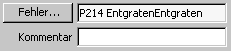
Die Definition der Fehler erfolgt im Modul Reklamation → unterer Modulreiter Grunddaten → oberer Modulreiter Fehler.
Zusätzlich können bei der Erfassung der Gut-/Schlechtstück auf dem Zeiterfassungsterminal auch die Fehlernummern angegeben werden. Sind auf einem Los Fehler erfasst, so wird in der Nachkalkulation ein Hinweis zu vorhandenen Fehlern angezeigt.
Zusätzlich werden im Ausdruck der Nachkalkulation die Fehler detailliert aufgeführt.
Rüstlager
Im Folgenden beschreiben wir ein Beispiel für Elektronik Bestückern z.B. EMS Dienstleister zum Aufbau eines Lagers direkt an den SMD Automaten. Das Rüstlager ist meist dadurch physikalisch abgebildet, dass direkt am SMD Automaten entsprechendes Material aufgerüstet ist. Gegebenenfalls möchten Sie sehen, wo sich welche Rolle des gleichen Bauteiles befindet. Daher werden die entnommenen Rollen auf das Rüstlager umgebucht.
Um dies abzubilden gibt es folgende Varianten.
Variante 1 - Materialbuchung bei Ausgabe
Es wird die Stückliste so eingestellt, dass keine Materialbuchung bei Losausgabe gemacht wird. Es wird ev. auch der zusätzliche Losstatus, Ausgegeben, der ja vor dem In Produktion kommt, aktiviert.
Werden nun Bauteile für das Rüsten des SMD Automaten benötigt, wird das Material, die ganze Rolle (also 5.000 Stück, auch wenn nur 100 benötigt werden) in das Los gebucht. Ist das Los fertig, muss es in der Regel wieder abgerüstet werden, vor allem auch um die Anzahl der verworfenen Bauteile tatsächlich zu erkennen. Es werden die Mengen ans Lager zurückgegeben, die übrig geblieben sind.
Eine Vereinfachung ist, dass man jede (Bauteil-) Rolle mit einer Reel-ID kennzeichnet. Ihr Bauteil ist damit chargengeführt und jede Rolle erhält eine automatisch vergebene Chargennummer. Damit spart man sich das zurückzählen, denn wenn die Rolle aus ist, klickt man im HELIUM 5 auf Charge vollständig verbrauchen und das HELIUM 5 bucht die noch lagernden Teile anteilig auf die betroffenen Lose.
Untervariante: Man bucht das Material automatisch bei der Ausgabe und akzeptiert, dass die Menge, wenn nicht im Hauptlager, dann am Rüstautomaten ist. Spart enorm Zeit und über die Artikel-Statistik bzw. die Funktion Artikel, Info, Frei in Fertigung, sieht man wo es noch sein könnte. Machen die meisten unserer Anwender, weil alles andere viel zu viel Zeit kostet.
Variante 2 - Rüstlager
Als zweite Variante legen Sie pro Rüstwagen ein Rüstlager an. Man stellt die Lose so ein, dass sie nur von einem der Rüstlager abbuchen dürfen.
Nun legt man sich einen Ziellagerlieferschein an, also Hauptlager an Rüstlager und bucht im Ziellagerlieferschein die ganzen ausgegebenen Mengen. Wenn man nun das Los ausgibt, entnimmt es automatisch die Stückzahlen und reduziert das Rüstlager.
Dazu benötigt man in der Regel noch eine Darstellung welches Material man am Rüstlager noch benötigt. Das ist ein Sonderreport für den Druck des Losmaterials. Üblicherweise macht man diese Version für die zur Verfügungstellung des Materials für seine externen Fertigungsdienstleister.
Zusätzlich können Sie einen laufenden Rüst-Ziel-Lager Lieferschein machen, der z.B. nur monatlich oder Quartalsweise abgeschlossen wird.